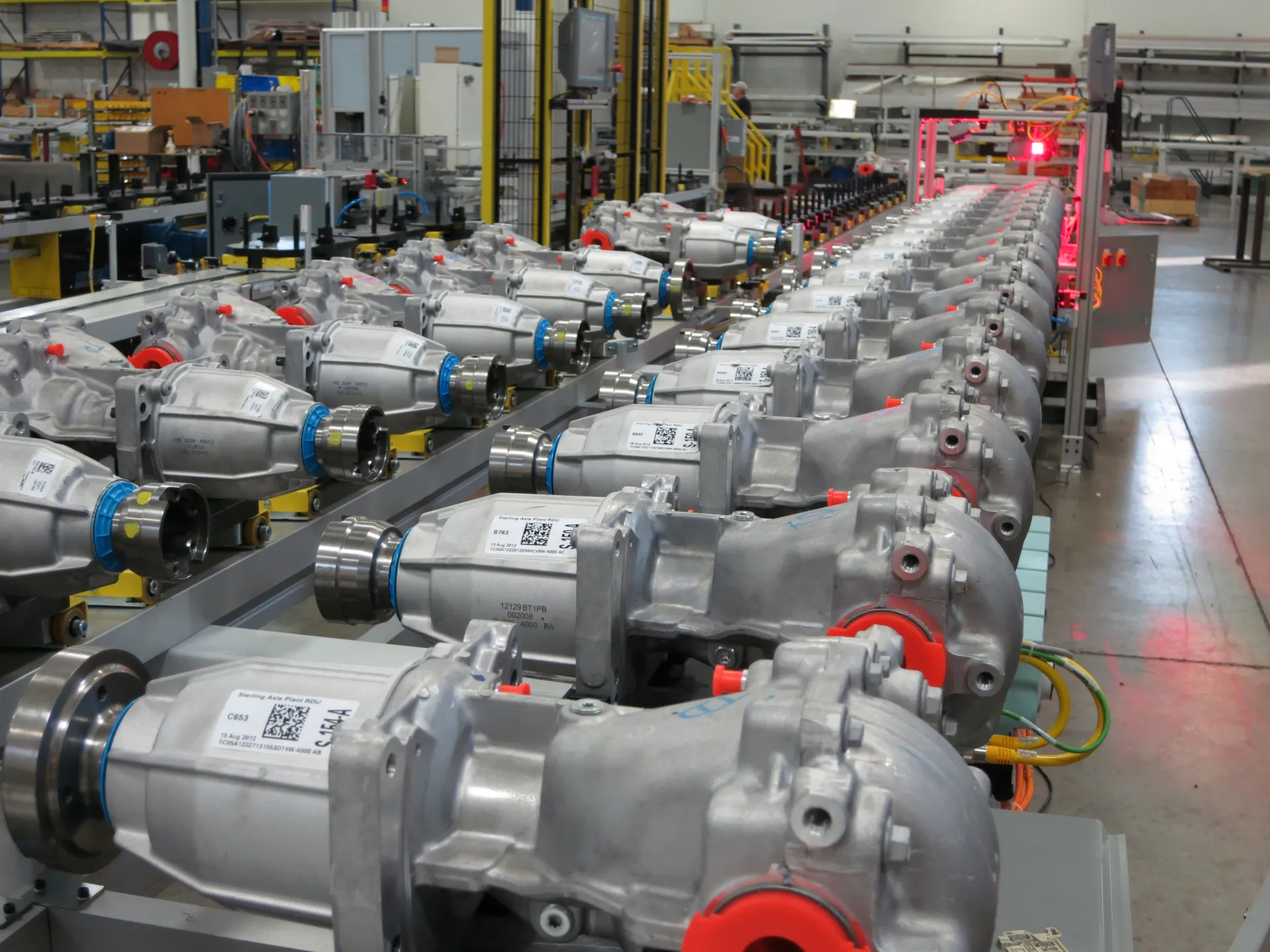
Warum Materialfluss so wichtig ist …
Im produzierenden Gewerbe herrscht stets ein Materialfluss. Ob das nun gewollt ist oder nicht oder ob das erstklassig gemanagt wird oder nicht. Wenn am Anfang ein bestimmtes Werkstück existiert und am Ende etwas anderes herauskommt, dann durchlief dieses Produkt verschiedene Prozesse innerhalb eines Materialflusses. Das wussten schon die Pioniere auf dem Gebiet, Henry Ford und Taichi Ohno, die beide sich den Materialfluss mit ihrer Philosophie zunutze gemacht und für sich optimiert haben.
In diesem Artikel sagen wir Ihnen, wieso der Materialfluss so wichtig ist und worauf Sie beim Management achten sollten.
In einer Produktionsstätte vor unserer Zeit. Die Pioniere des Materialflusses.
Zu Beginn des 20. Jahrhunderts waren an dem gleichzeitig einhergehenden Auftrieb der weltweiten Wirtschaft einige Menschen federführend beteiligt und haben die Art der Produktion nachhaltig verändert. Jeder auf seine Art.
Henry Ford, der mit seinem Produktionsmanagement den Grundstein für die Massenproduktion auf Basis von Fördersystemen legte, hatte zur damaligen Zeit ein System entwickelt, welches darauf ausgelegt war, so schnell wie möglich einen Mehrwert zu schaffen. Das bedeutet, keine Puffer innerhalb der Fertigungslinie, keine Varianten beim Produkt und alles in einem vorgeschriebenen Ablauf.
„Jeder Kunde kann seinen Wagen in jeder Farbe lackieren lassen, solange sie schwarz ist“ steht sinnbildlich für die Herangehensweise des amerikanischen Pioniers. Dies funktioniert auch hervorragend, solang es keine Ausfälle innerhalb der Produktionslinie gibt oder die Kunden keine Extrawünsche haben oder Varianten zu fertigen sind. Doch so einfach ist es eben nicht.
Taichi Ohno, der das Toyota-Produktionssystem schuf, wählte einen anderen Ansatz, der auch heute noch den Ansprüchen moderner Kunden gerecht wird. Er konzentrierte sich mehr auf den Materialfluss – also, der Eliminierung von Störungen und die Reduzierung von Werkstücken im Umlauf der Fertigung (WIP).
Die heute sogenannte „Lean“-Produktion zeichnet sich dahin gehend aus, dass es sich genau im Kundentakt befindet und erst produziert wird, wenn es eine direkte Nachfrage gibt. Auch bekannt als Pull-Prinzip.
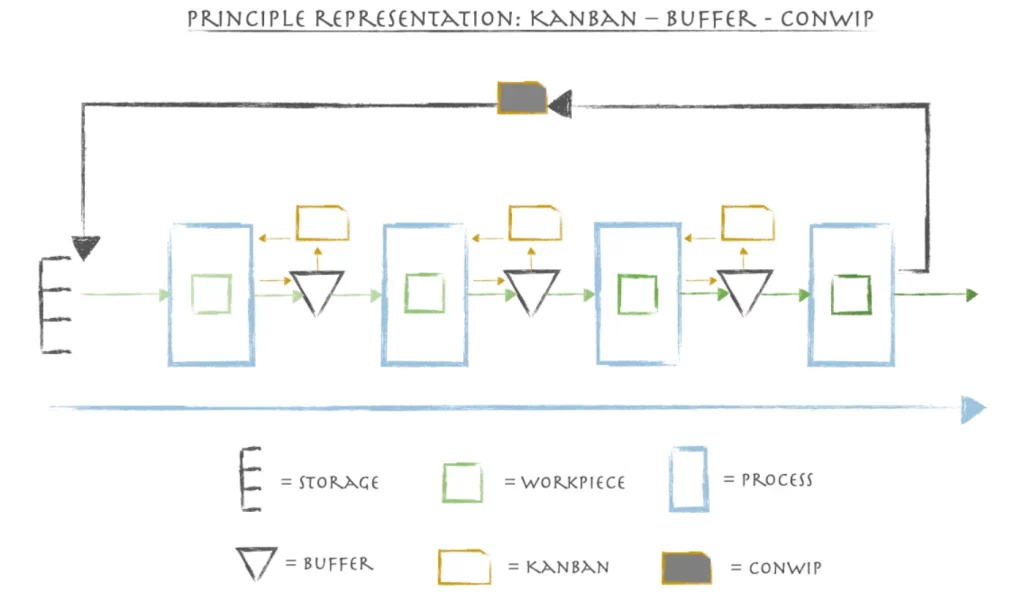
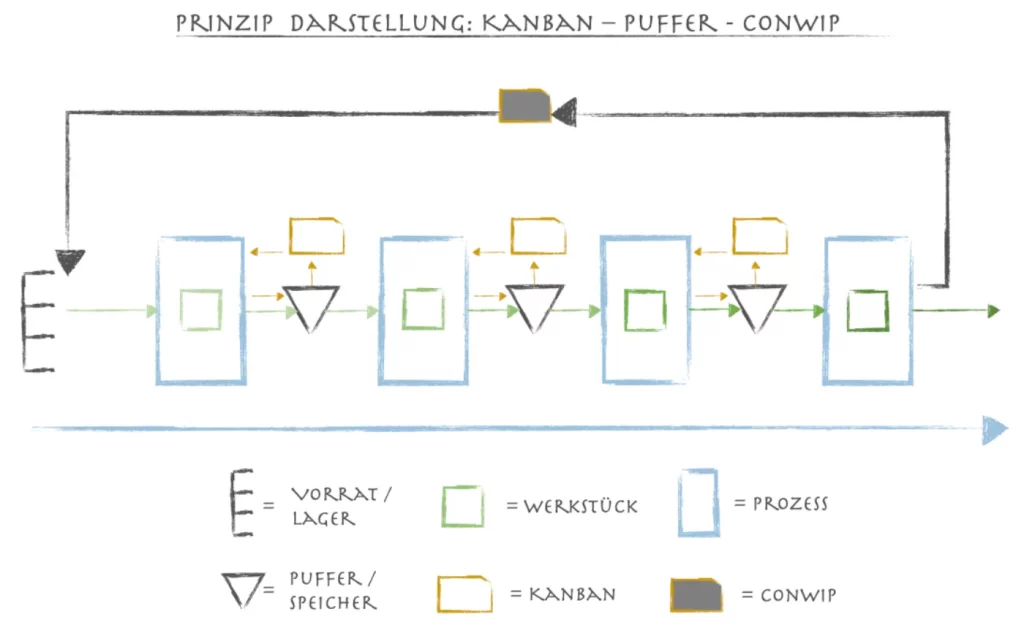
Das große Ziel: Schnelligkeit
Ziel eines jeden Unternehmens in der Fertigungsindustrie muss sein, die jeweiligen Werkstücke durch eine bestimmte Bearbeitung, Weiterverarbeitung oder Zusammenführung mit anderen Teilen zum neuen und letztlichen Endprodukt zu machen – bestenfalls schnell. Jede Minute, die ein Produkt im Werk und nicht im Verkauf oder beim Kunden liegt, ist gebundenes Kapital. Daher ist auch das oberste Ziel, die Werkstücke so schnell wie möglich durch die Fertigungslinie zu bringen.
Der Materialfluss spielt an der Stelle dementsprechend eine wichtige Rolle.
- Wie ist die Produktion aufgebaut?
- Welche Stelle in der Produktion ist das schwächste Glied?
- Wo besteht Optimierungsbedarf?
- Was passiert, wenn kurzfristig eine Maschine oder Mitarbeiter ausfallen?
Diese und viele weitere Fragen, müssen sich fortlaufend gestellt werden, um wirklich das meiste aus der eigenen Produktionsstätte herauszuholen.
Weniger Work in Process für mehr Qualität
Fakt ist: Jede Sekunde, die ein Werkstück in einem Zwischenlager verbringt, verursacht Kosten – für Lagerpersonal, für die Logistik im Allgemeinen und für die Qualitätssicherung. Gelagerte Werkstücke können natürlich fehlerbehaftet sein. Die Qualitätskontrolle der Teile benötigt Zeit und Geld. Oftmals ist es so, dass der Part der Qualitätskontrolle zum Engpass in der gesamten Fertigung wird – also der Part, der dafür verantwortlich ist, dass eine Überproduktion entsteht und diese immer größer wird, wenn der Materialfluss nicht optimiert wird.

Im Allgemeinen lässt sich daher sagen, dass die eigentliche reine Bearbeitungszeit der Werkstücke nur ein Bruchteil von dem ist, wie viel Zeit die Werkstücke im Zwischenlager verbringen.

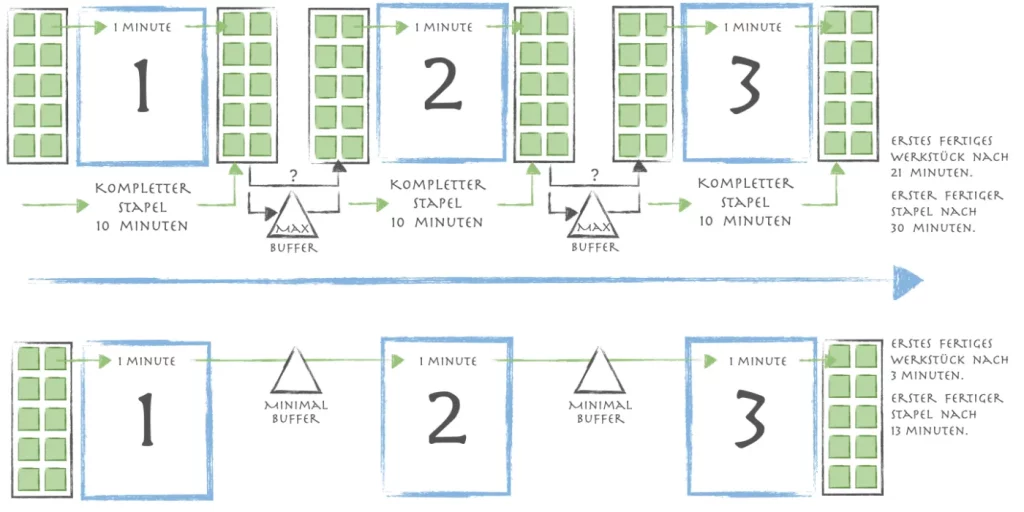
Anhand des Schaubilds erkennen Sie, wie viel länger es braucht, wenn feste Puffer mit einer Anzahl an Teilen zwischen den Prozessen bestehen. 21 Minuten vs. 3 Minuten für das erste Teil und 30 Minuten vs. 13 Minuten für einen kompletten Satz von zehn Teilen.
→ WIP beeinflusst Lead-Time und Throughput
Wie Sie die Lead-Time der Werkstücke im Valuestream berechnen, erfahren Sie hier.
Puffer im Materialfluss kann auch gut sein
Nun wäre es jedoch falsch zu sagen, dass Zwischenlagerungen oder Puffer generell schlecht für die Profitabilität sind. Denn mit den richtigen Puffern an den richtigen Stellen, um Fluktuationen aufzufangen, kann der Materialfluss und damit einhergehend die Wertschöpfung der gesamten Produktion verbessert werden. Dies führt wiederum zu einem Vorteil gegenüber den Wettbewerbern, da so die gesamte Durchlaufzeit abnimmt.
Der grundlegende Gedanke sollte dabei stets sein, dass ein einwandfreier Materialfluss zwischen den einzelnen Produktionsprozessen innerhalb einer Fertigungslinie der effizienteste Weg ist, die Produktions- und Lieferzeiten zu verkürzen.
Nicht die einzelne Maschine, sondern das große Ganze.
Somit macht der Fokus auf die Verbesserung einzelner Maschinen wenig Sinn, wenn die davor und dahinter liegenden Produktionsschritte nicht darauf abgestimmt sind. Das Ergebnis wäre demnach eher kontraproduktiv. So kann es nämlich passieren, dass die neue, verbesserte Maschine so schnell über den Bedarf hinaus produziert, dass sich an anderen Stellen größere Mengen an Werkstücken sammeln und wieder das vorab erwähnte Problem eintritt – zu lange Wartezeiten von Werkstücken innerhalb der Produktion und somit gebundenes Kapital im Werk.
Wird hingegen das große Ganz betrachtet, kann systematisch an mehreren Stellen optimiert werden, sodass die einzelnen Schritte – passend zur jeweiligen Kapazität und unter Berücksichtigung des Engpasses (Bottlenecks) – immer aufeinander abgestimmt sind.
Fazit: Der SmartFlow-Effect
Über die Engpasstheorie (ToC) wird das schwächste Glied in der Produktionslinie erkannt, am besten sogar bestimmt, mithilfe dessen die gesamte Geschwindigkeit der Fertigung orgegeben wird. Mithilfe einer hybriden Pull-Kombination aus den beiden Lean-Methoden Kanban und CONWIP wird die Anzahl der Werkstücke im Ablauf kontrolliert reduziert, was zur Folge hat, dass auch die Durchlaufzeit verkürzt wird und alle Prozesse trotzdem weiterhin mit Werkstücken versorgt sind.
Auf diese Weise erreicht man den sogenannten SmartFlow-Effect. Völlig ohne anfängliche Investitionen in intelligente KI-Systeme oder Veränderungen an den Produktionsgeschwindigkeiten einzelner Maschinen.
Mit einfacher und intelligenter Herangehensweise an die Fertigungslinie lässt sich der Materialfluss verbessern, die Produktion steigern und die Wettbewerbsfähigkeit erhöhen.
Möchten Sie mehr über die Funktionsweise des SmartFlow-Effects erfahren? Sprechen Sie uns gerne an. Wir erklären Ihnen, wie er funktioniert und wie auch Sie ihn erreichen.