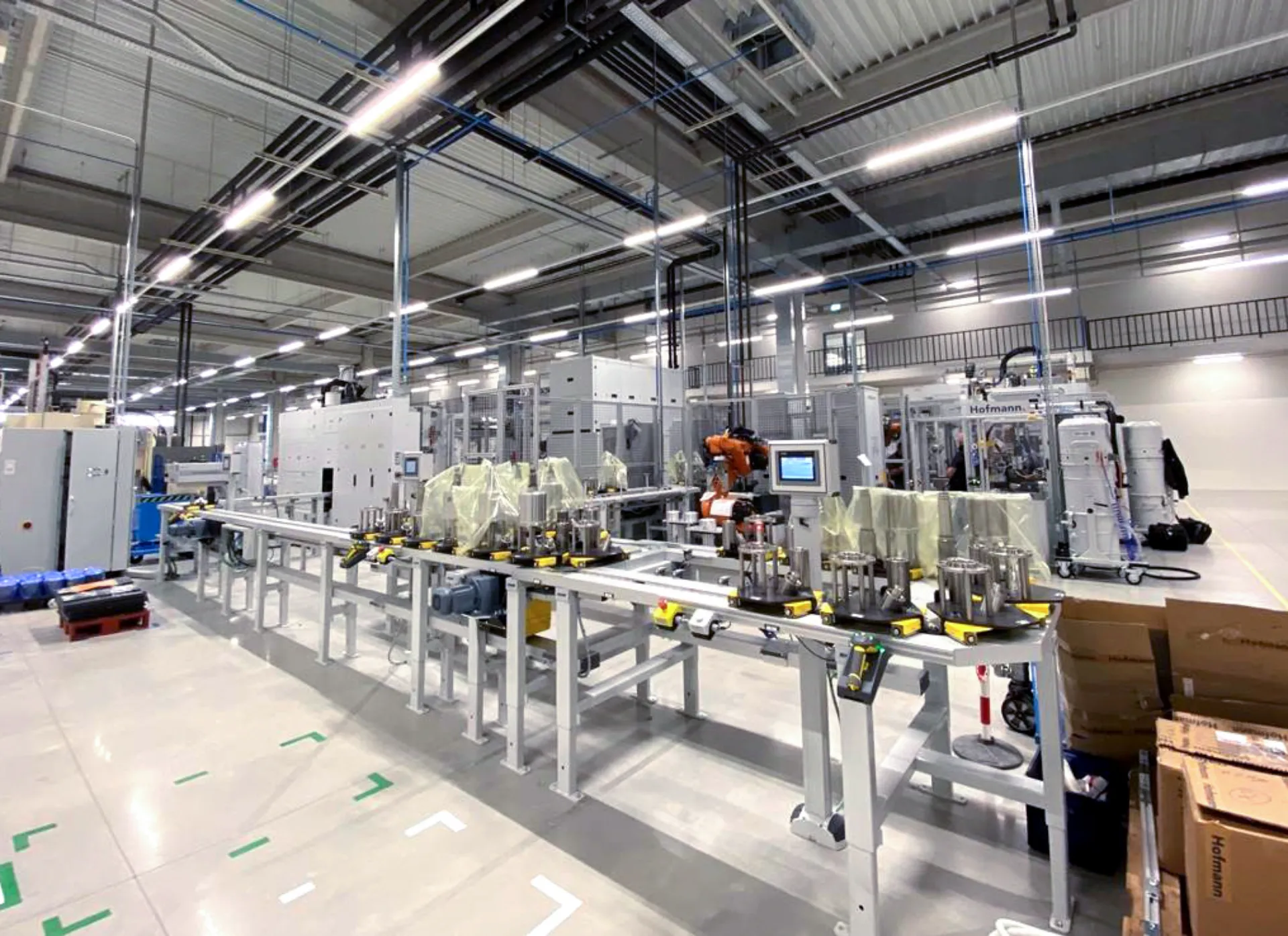
Neuer Materialfluss – so funktioniert die Implementierung
Eines der bedeutendsten Erfindungen der Menschheit ist mit großer Sicherheit der Computer. Ohne die Computertechnologie wäre das heutige Kommunikationszeitalter, in dem wir uns befinden, überhaupt nicht möglich. Nicht nur im privaten Leben, auch auf beruflicher Ebene ist der Computer nicht mehr wegzudenken.
In der produzierenden Industrie und vielen weiteren spielt die Computertechnologie eine wichtige Rolle. CAD-Software – also Computer Aided Design – wird gerne als technisches Hilfsmittel zur Erstellung von Konstruktionszeichnungen und Bauplänen verwendet. Ob, 2D- oder 3D-Modellierung, CAD als Planungstool ist nicht mehr aus der Arbeit von Technikern, Konstrukteuren, Architekten oder Bauzeichnern wegzudenken.
So sehr diese Computerunterstützung auch benötigt wird, alles kann und soll sie nicht ersetzen. Für die Planung des Materialflusses darf nicht der Fehler begangen werden, dass mithilfe solcher Technologien die allseits beste Lösung gefunden wird. Oftmals ist zu Beginn der Planung von Produktionslinien Papier und Stift die bessere Wahl.
Den richtigen Anfang finden
Die Einführung einer neuen Produktionslinie ist durchaus komplex und zeitaufwendig. Ebendarum ist es notwendig, schon zu Beginn mit den richtigen Arbeitsschritten zu beginnen, um nicht im Nachhinein das böse Erwachen zu erleben und kosten- sowie zeitintensive Umplanungen oder Umbaumaßnahmen vollziehen zu müssen.
Viele Techniker und Konstrukteure nutzen direkt zum Start des Aufbauprozesses CAD als Werkzeug. Dies führt dazu, dass sich direkt auf die einzelnen Prozesse, den benötigten Platzbedarf und die Ausrichtung der jeweiligen Maschinen konzentriert wird.
Dies ist nicht per se falsch, jedoch wird bei dieser Vorgehensweise eine wichtige Sache vernachlässigt – der Materialfluss. Wie und wie schnell bewegen sich die einzelnen zu produzierenden Werkstücke durch das Produktionssystem?
Die einzelnen Maschinen sind laut Aufstellplan innerhalb der CAD-Software optimal zueinander und auf den Platzbedarf abgestimmt. Ob dies jedoch dem allgemeinen Wertstrom zugutekommt, steht auf einem ganz anderen Blatt Papier.
Den Menschen im Wertstrom nicht vergessen
Werden die ersten Gedanken also erst einmal ausschließlich auf die Maschinen verwendet, werden künftig negative Folgen auftreten.
Was ist etwa, wenn eine Maschine plötzlich ausfällt und nicht weiter produzieren kann? Es kommt nicht selten vor, dass der Ausfall einer einzelnen Maschine den gesamten Valuestream lahm legt, bis diese wieder voll funktionstüchtig ist.
Hinzu kommt, dass, trotz aller technischen Hilfsmittel, an vielen Stellen im System Menschen arbeiten. Auch diese dürfen bei der Planung nicht außer Acht gelassen werden. Ist der Aufbau der Anlage zwar für die Maschinen bestmöglich berechnet, jedoch nicht für den Materialfluss und die effiziente Arbeitsweise der Mitarbeiter, kommt schnell Frust unter der Belegschaft auf. Für die Maschinen mag der eine oder andere Aufbau sinnvoll erscheinen, wenn die Menschen im System jedoch viele für sie unsinnige Schritte gehen müssen oder die Kommunikation untereinander schlecht bis gar nicht möglich ist, ist das nicht förderlich für eine motivierende Arbeitsleistung und die Produktionsgeschwindigkeit.
Papier und Stift – oftmals die geeignetere Wahl
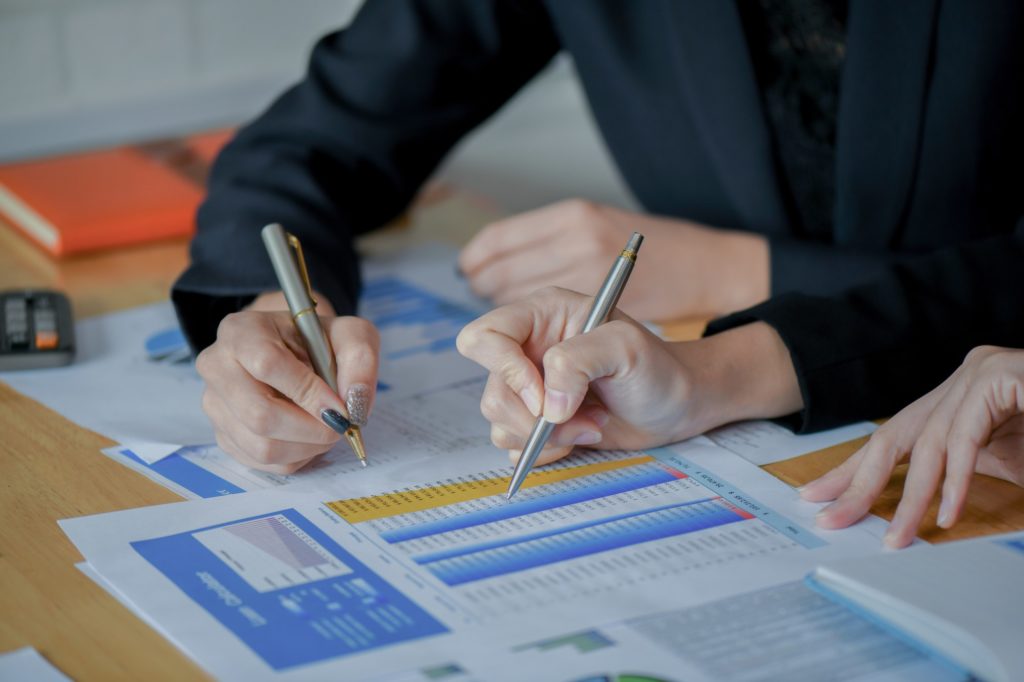
Also, CAD ist unerlässlich für eine erfolgreiche Produktion, jedoch noch nicht am Anfang der Planung. An der Stelle ist es wichtiger, den optimalen Materialfluss im Fokus zu haben.
Wie gelangen die Werkstücke durch die einzelnen Maschinen und Puffer durch das System, bis das gewünschte Endprodukt entstanden ist?
Dies ist die erste Frage, die Sie sich als Techniker, Planer oder Projektverantwortlicher stellen müssen. Die beiden wichtigsten Arbeitsmaterialien sind an dieser Stelle tatsächlich Papier und Stift.
Mit einfachsten Mitteln die perfekte Materialfluss-Planung
Mithilfe von Papier und Stift lassen sich tatsächlich viele wichtige Dinge vorab planen, die mit dem Materialfluss zu tun haben.
Als Beispiel nehmen wir eine Fertigungslinie auf der, aus einer Teilefamilie, mehrere Varianten oder auch ähnliche Teile in größeren Stückzahlen gefertigt werden sollen. Solche Linien werden mit ‚High Volume / High Mix‘ beschrieben und zählen zu den komplexesten Aufgaben in der Materialflussplanung.
- Für eine Übersicht tragen sie alle ihre Teile, mit Bezeichnung, Varianten oder Teilenummer in die erste Spalte einer Tabelle ein.
- In die zweite Spalte notieren sie deren Stückzahl, die produziert werden soll.
- In der Kopfzeile der jeweiligen weiteren Spalten tragen sie, möglichst in der Bearbeitungsreihenfolge, die Prozesse ein, die benötigt werden.
- Wenn sie jetzt die Teilezeilen nach Prozess durchgehen und bei jedem Prozess, den sie für das jeweilige Teil benötigen, ein Kreuz machen, bekommen sie einen visuellen Überblick über gute oder schlechte Prozessübereinstimmung.
- Markieren Sie die Zeilen der Werkstücke, bei denen die Prozesse gut zueinanderpassen und summieren Sie die Stückzahlen, um eine Gesamtkapazität der Linie zu erhalten. Falls diese zu hoch oder die Prozesskette zu lang erscheint, sollten sie die Linie in zwei oder drei eigenständige aufteilen.
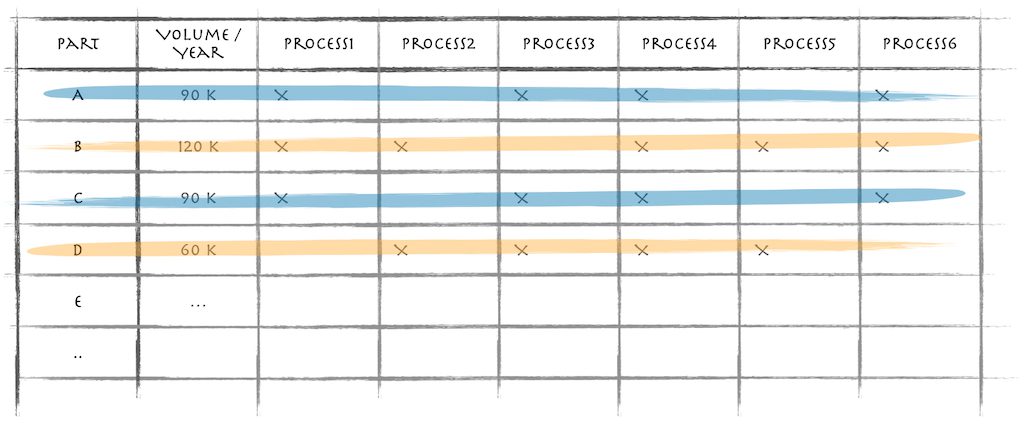
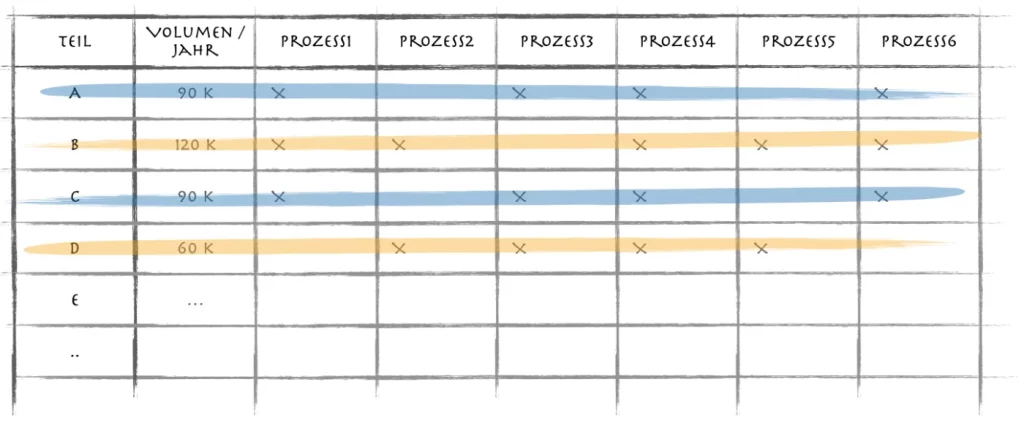
Nächster Schritt: Kapazitäten-Planung
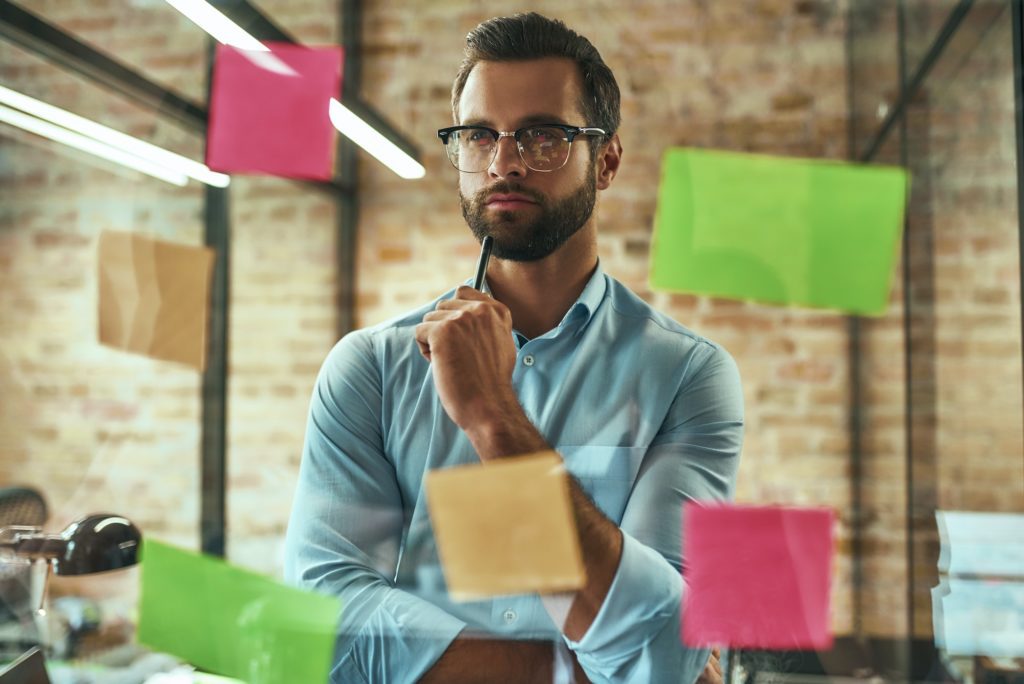
Indessen ist es eine Wunschvorstellung, dass mithilfe einer einzelnen Tabelle der gesamte Produktionsbetrieb aufgenommen werden kann und alle glücklich damit sind. Im folgenden Schritt kommt demnach die Planung der zur Verfügung stehenden Kapazitäten in der Produktionsstätte.
- Welche Maschinen werden benötigt?
- Wie viel Zeit wird für die jeweiligen Produktionsschritte benötigt?
- Wie viele Maschinen werden für die einzelnen Prozesse benötigt?
- Wie verbinde ich diese und schaffe den nötigen Puffer?
Die und noch weitere Fragen werden Sie sich an der Stelle nun stellen. Denn die Kapazitäten stimmen oftmals nicht mit den vorab getätigten theoretischen Planungen überein und führen eher zu Beschränkungen, welche Werkstücke wirklich gemeinsam gefertigt werden können.
An der Stelle wird die Produktionszeit hinzugezogen.
Tragen Sie also neben den Kreuzen die Prozesszeiten ein, die für den jeweiligen Prozess und das Werkstück benötigt werden. Anschließend werden diese Prozess-Taktzeiten benötigt, um herauszufinden, wie hoch die Anzahl der Werkstücke (Volumen) ist, die in der verfügbaren Arbeitszeit gefertigt werden können.
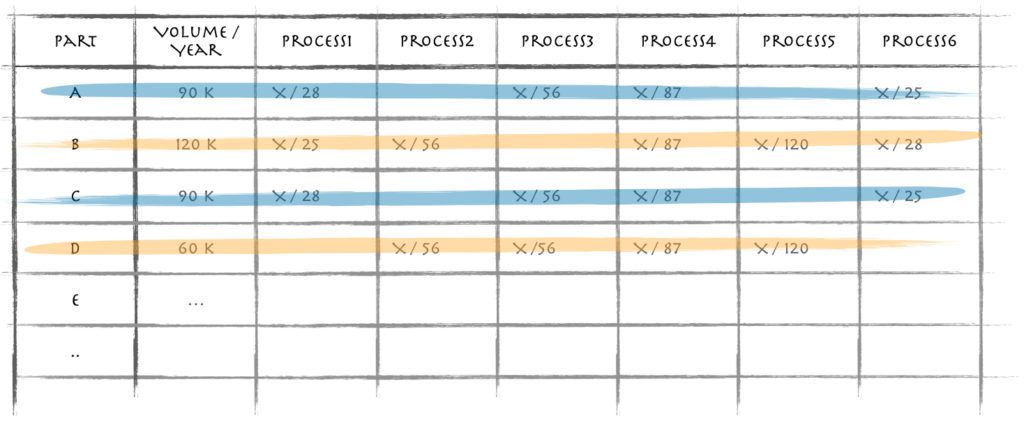
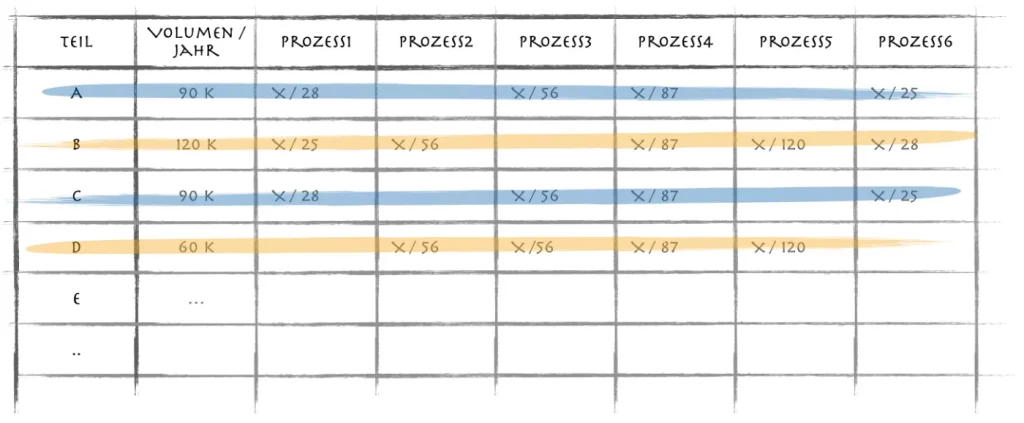
Definieren Sie nun die effektive Arbeitszeit, die Ihnen für die Fertigung der Werkstücke zur Verfügung steht. Geben Sie z.B. sieben Stunden für eine Schicht am Tag an und rechnen mit 235 Arbeitstagen, so ergibt das eine Prozess-Taktzeit, in unserem Beispiel, von circa maximal 33 Sekunden.
Effektive Arbeitszeit : Volumen = Taktzeit
Überschreitet nun die Prozess-Taktzeit den ermittelten Maximalwert, sind mehrere, parallel geschaltete Ressourcen (Maschinen) für einen Prozess erforderlich. So würde der Prozess 5 mit 120 Sekunden Prozesszeit insgesamt 4 Ressourcen benötigen.
(120 / 33 = 3,6 = 4)
Der dritte Schritt in der Planung: das Prozessflussdiagramm
Mithilfe der Übersicht und der ermittelten Anzahl von Ressourcen sind Sie in der Lage ein Prozessflussdiagramm zu erstellen. Darin wird die gesamte Fertigungslinie, unter der Berücksichtigung von kurzen Durchlaufzeiten, sowie die angedachten Puffer vor und nach den Maschinen dargestellt.
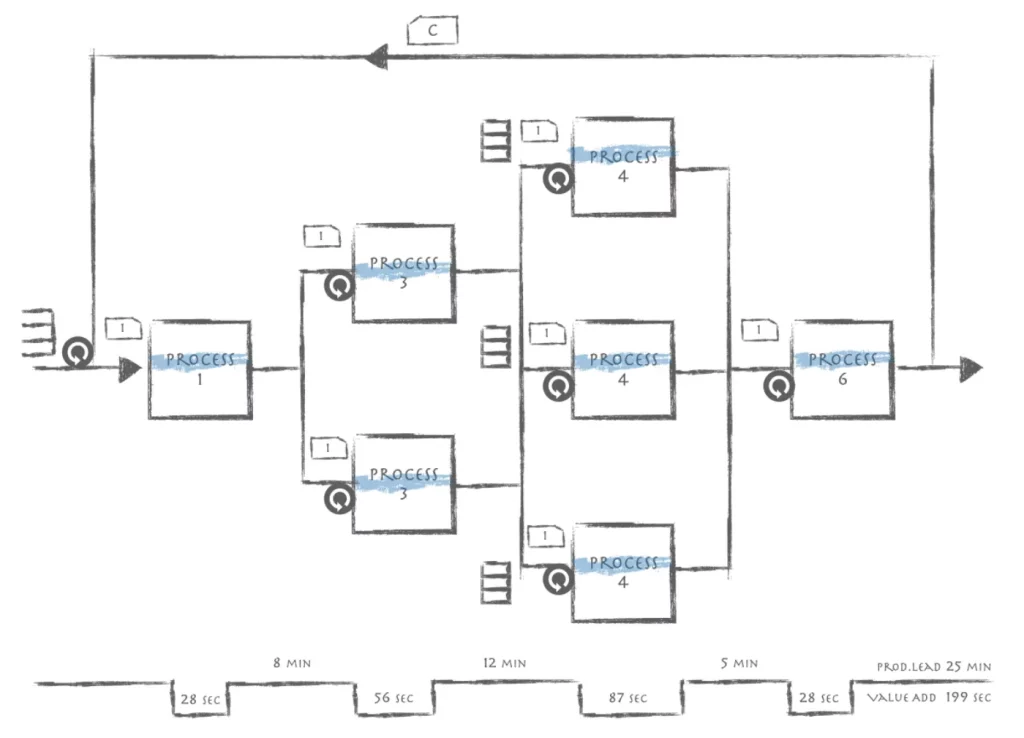
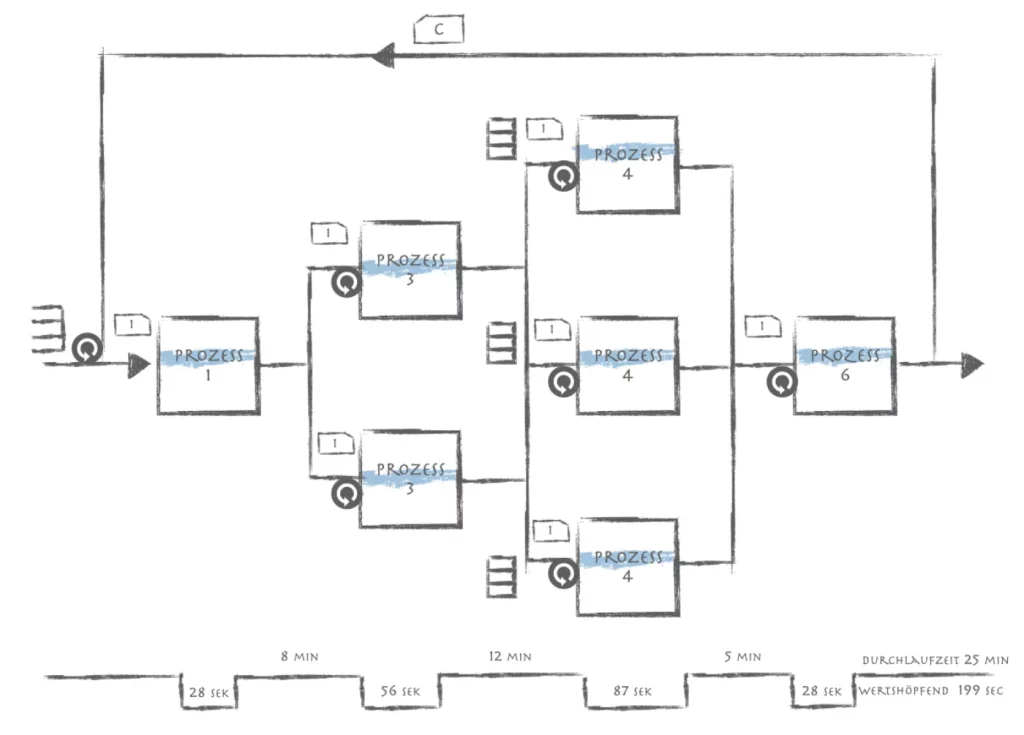
Durch die Zuhilfenahme von Wertstromsymbolen lenken Sie den Fokus auf kurze Durchlaufzeiten und kleine Zwischenspeicher an den richtigen Stellen. In unserem Beispiel haben wir natürlich den Smartflow-Effect mit Kanban / ConWiP und, durch die Festlegung der Taktzeiten, den Bottleneck laut ToC (Theory of Constrains) eingebaut.
Nun erstellen Sie mit diesem Prozessflussdiagramm ein Blocklayout und entwickeln Sie den Materialfluss so, dass für jedes Teammitglied klar ist, wie die Werkstücke durch die Maschinen und die Puffer gelangen. Damit haben sie einen Wertestrom, wo ihr Material im Fluss ist.
Fazit: Computer sind wundervoll, aber …
Anhand der kurzen Beschreibung in der Prozessplanung Ihres Materialflusses erkennen Sie, dass die Hinzunahme von CAD im Laufe des Produktionsprozesses mittlerweile zwar unabdingbar geworden ist, diese jedoch zur richtigen Zeit hinzugezogen werden muss.
Wird bereits bei der Planung der Produktionsstätte der Fokus auf die falschen Dinge gelegt, können im Fertigungsprozess schwerwiegende Fehler auftreten, die hätten verhindert werden können.
Beziehen Sie bei der Produktionsplanung direkt zu Beginn den Materialfluss mit ein und richten Sie die ersten Schritte darauf aus. Erst wenn Sie wissen, wie die Werkstücke innerhalb Ihres Systems voranschreiten, welche Zeit diese benötigen und wo Puffer eingebaut werden müssen, können Sie effektive Kombinationen erkennen, die ihre Produktionszeit drastisch kürzen. Dies verschafft Ihnen gegenüber Ihrer Konkurrenz einen erheblichen Vorteil.
Sie benötigen Unterstützung bei der Planung Ihrer Fertigungslinie oder bei der Implementierung des Materialflusses? Sprechen Sie uns gerne an. Wir helfen Ihnen dabei und zeigen Ihnen, wie Sie mit dem SmartFlow-Effect zum Branchenführer werden.