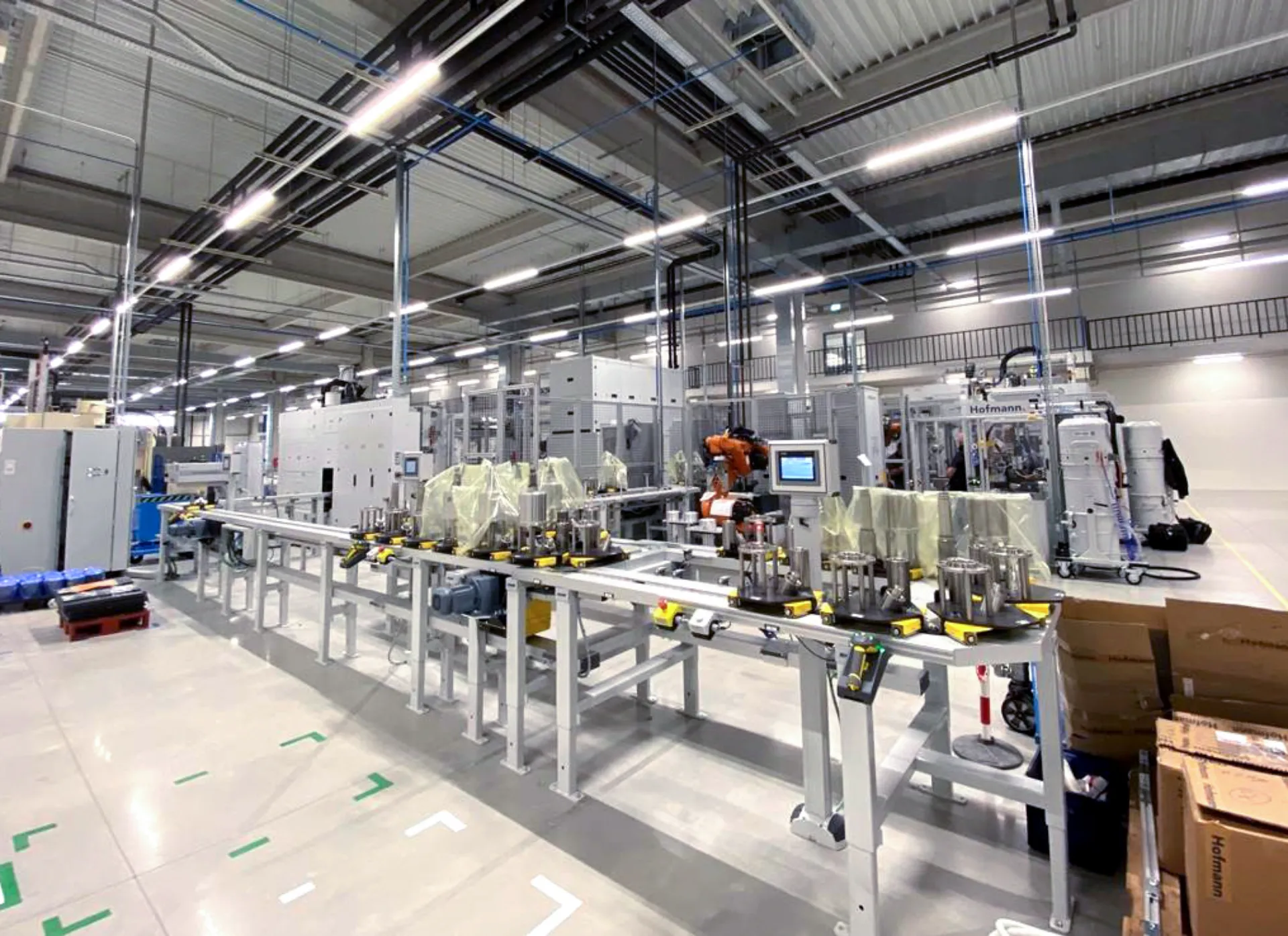
New material flow - this is how implementation works
One of the most significant inventions of mankind is almost certainly the computer. Without computer technology, the communication age in which we find ourselves today would not be possible at all. Not only in private life, but also on a professional level, the computer has become indispensable.
Computer technology plays an important role in the manufacturing industry and many others. CAD software - i.e. Computer Aided Design - is popularly used as a technical tool for creating construction drawings and blueprints. Whether, 2D or 3D modeling, CAD as a planning tool is no longer imaginable without the work of technicians, designers, architects or draftsmen.
As much as this computer support is needed, it cannot and should not replace everything. For the planning of the material flow, the mistake must not be made that the all-round best solution is found with the help of such technologies. Often, paper and pencil is the better choice at the beginning of production line planning.
Finding the right beginning
The introduction of a new production line is complex and time-consuming. This is why it is necessary to start with the right steps right at the beginning in order to avoid a rude awakening later on and having to carry out costly and time-consuming rescheduling or conversion measures.
Many engineers and designers use CAD as a tool right at the start of the build process. This leads to a direct focus on the individual processes, the space required and the alignment of the respective machines.
This is not wrong per se, but this approach neglects one important thing - the material flow. How and how fast do the individual workpieces to be produced move through the production system?
According to the layout plan within the CAD software, the individual machines are optimally coordinated with each other and with the space requirements. However, whether this benefits the general value stream is a different matter altogether.
Don't forget the people in the value stream
So, once the initial thoughts are spent exclusively on the machines, negative consequences will occur in the future.
What happens if a machine suddenly breaks down and cannot continue production? It is not uncommon for the failure of a single machine to paralyze the entire Valuestream until it is fully functional again.
In addition, despite all the technical aids, people work at many points in the system. These must also not be disregarded during planning. If the layout of the system is calculated in the best possible way for the machines, but not for the material flow and the efficient working methods of the employees, frustration quickly arises among the workforce. For the machines, one or the other set-up may seem sensible, but if the people in the system have to go through many steps that make no sense to them, or if communication with each other is poor or even impossible, this is not conducive to a motivating work performance and production speed.
Paper and pen - often the more suitable choice
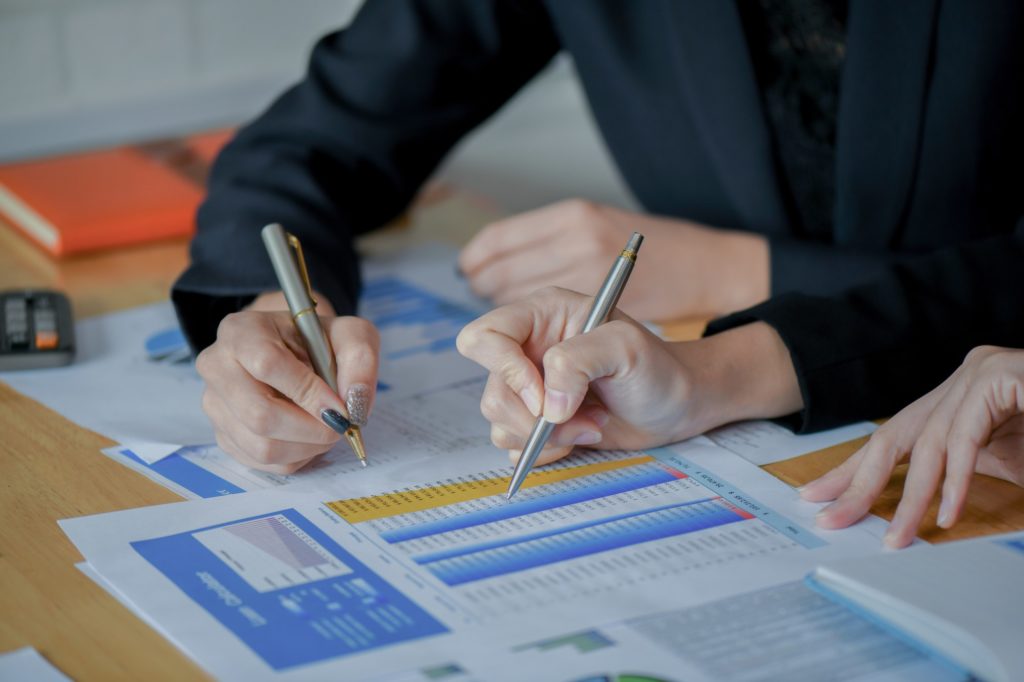
So, CAD is essential for successful production, but not yet at the beginning of planning. At this point, it is more important to focus on the optimal material flow.
How do the workpieces pass through the individual machines and buffers until the desired end product is created?
This is the first question you need to ask yourself as a technician, planner or project manager. The two most important working materials at this point are actually paper and pen.
The perfect material flow planning with the simplest of means
With the help of paper and pencil, you can actually plan many important things in advance that have to do with the flow of materials.
As an example, let's take a production line on which, from a family of parts, several variants or similar parts are to be produced in larger quantities. Such lines are described as 'High Volume / High Mix' and are among the most complex tasks in material flow planning.
- For an overview, they enter all their parts, with designation, variants or part number in the first column of a table.
- In the second column, write down the number of pieces to be produced.
- In the header of the respective further columns they enter, if possible in the processing order, the processes that are required.
- Now, if they go through the part lines by process and put a cross by each process they need for that part, they will get a visual overview of good or bad process match.
- Mark the lines of workpieces where the processes fit well together and sum up the numbers of pieces to get a total capacity of the line. If this seems too high or the process chain too long, they should split the line into two or three independent.
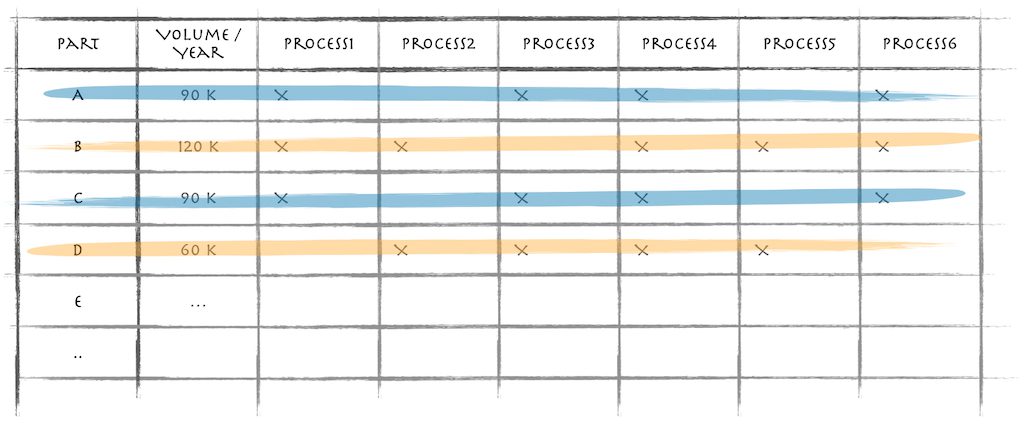
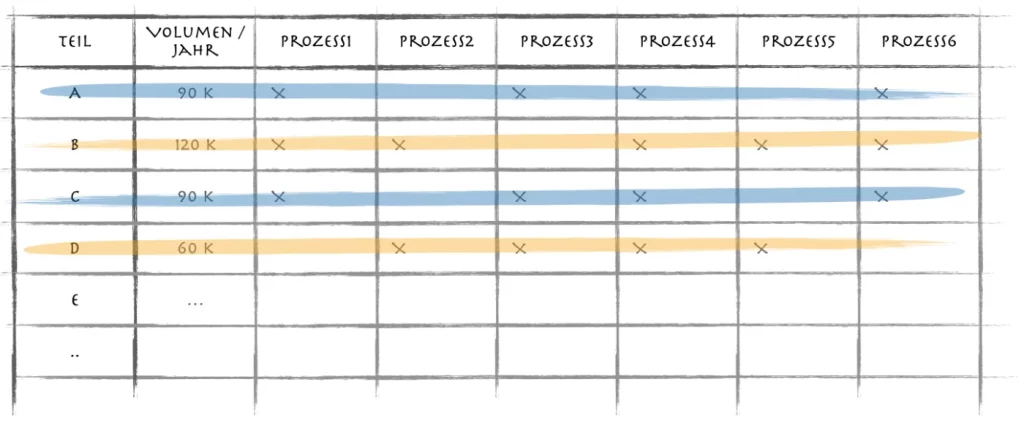
Next step: Capacity planning
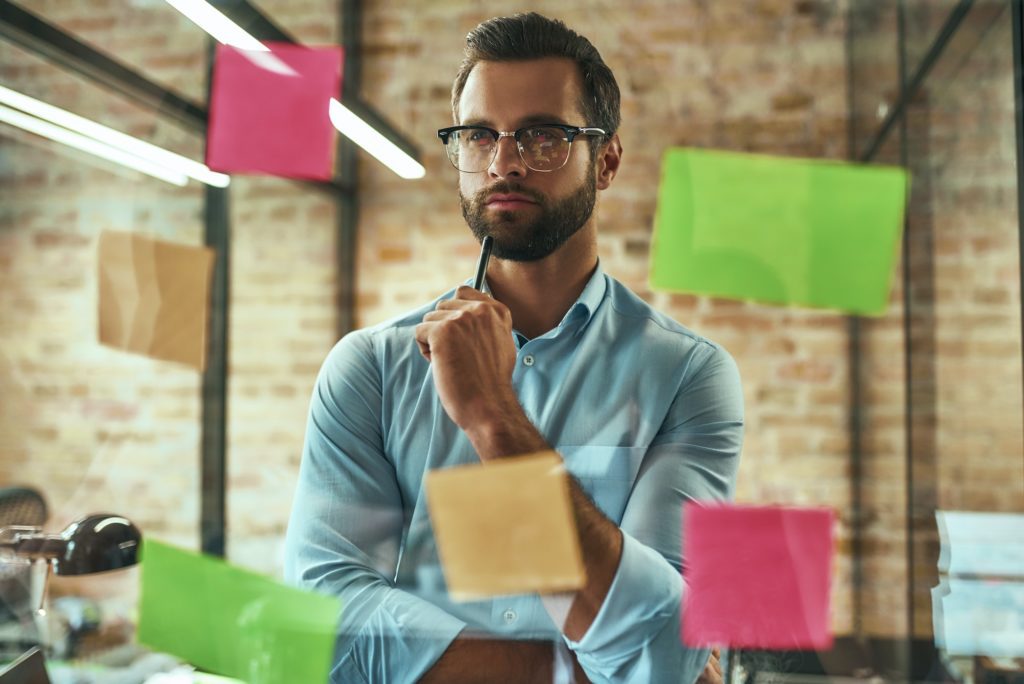
However, it is a wishful thinking that with the help of a single table the entire production operation can be started and everyone is happy with it. The next step is to plan the available capacities in the production facility.
- What machines are needed?
- How much time is needed for the respective production steps?
- How many machines are needed for each process?
- How do I connect them and create the necessary buffer?
You will now ask yourself these and other questions at this point. Because the capacities often do not match the theoretical plans made in advance and rather lead to restrictions as to which workpieces can really be manufactured together.
At this point, the production time is added.
So, next to the crosses, enter the process times that are needed for the respective process and workpiece. Subsequently, these process cycle times are needed to find out how many workpieces (volumes) can be produced in the available working time.
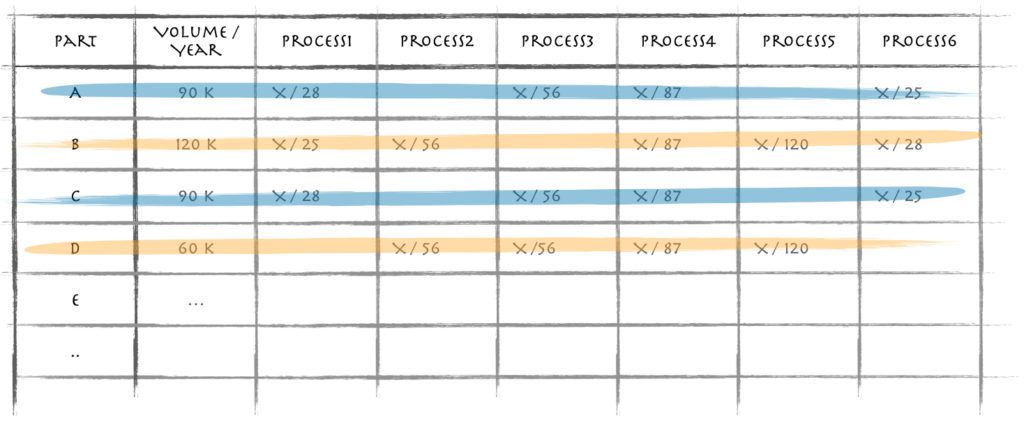
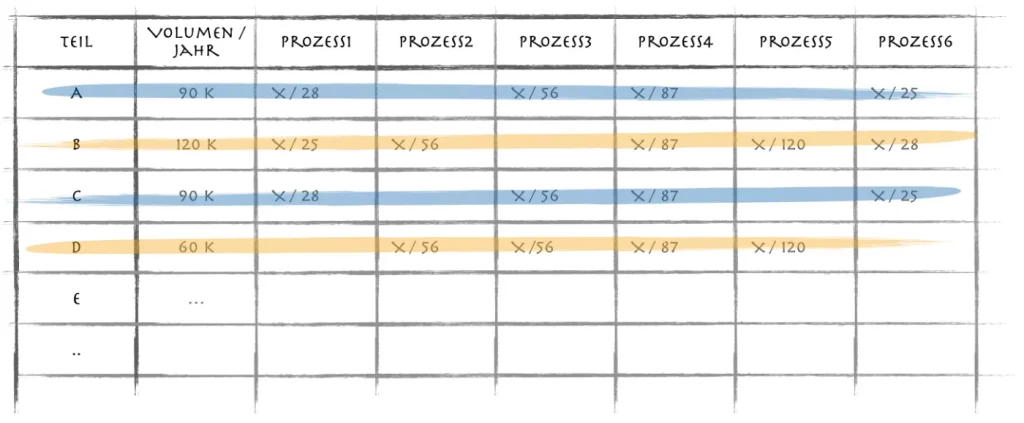
Now define the effective working time available to you for the production of the workpieces. If, for example, you specify seven hours for a shift per day and calculate 235 working days, this results in a process cycle time, in our example, of approximately 33 seconds maximum.
Effective working time : Volume = Takt time
If the process cycle time now exceeds the determined maximum value, several resources (machines) connected in parallel are required for a process. For example, process 5 with a process time of 120 seconds would require a total of 4 resources.
(120 / 33 = 3,6 = 4)
The third step in planning: the process flow diagram
With the help of the overview and the determined number of resources you are able to create a process flow diagram. This shows the entire production line, taking into account short lead times, as well as the planned buffers before and after the machines.
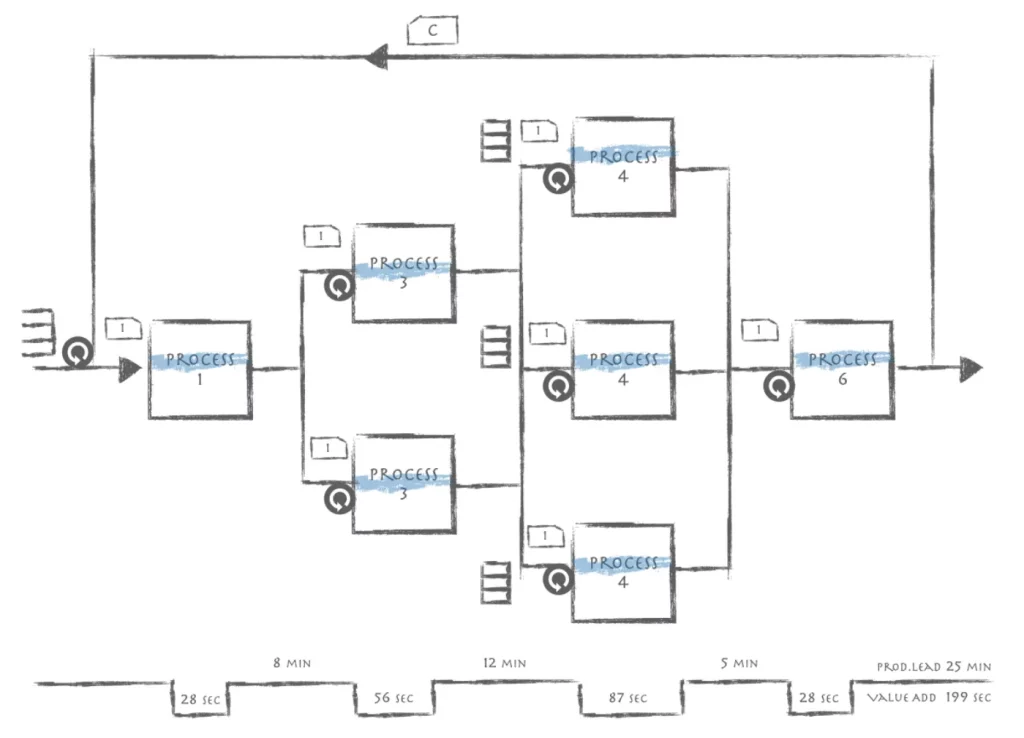
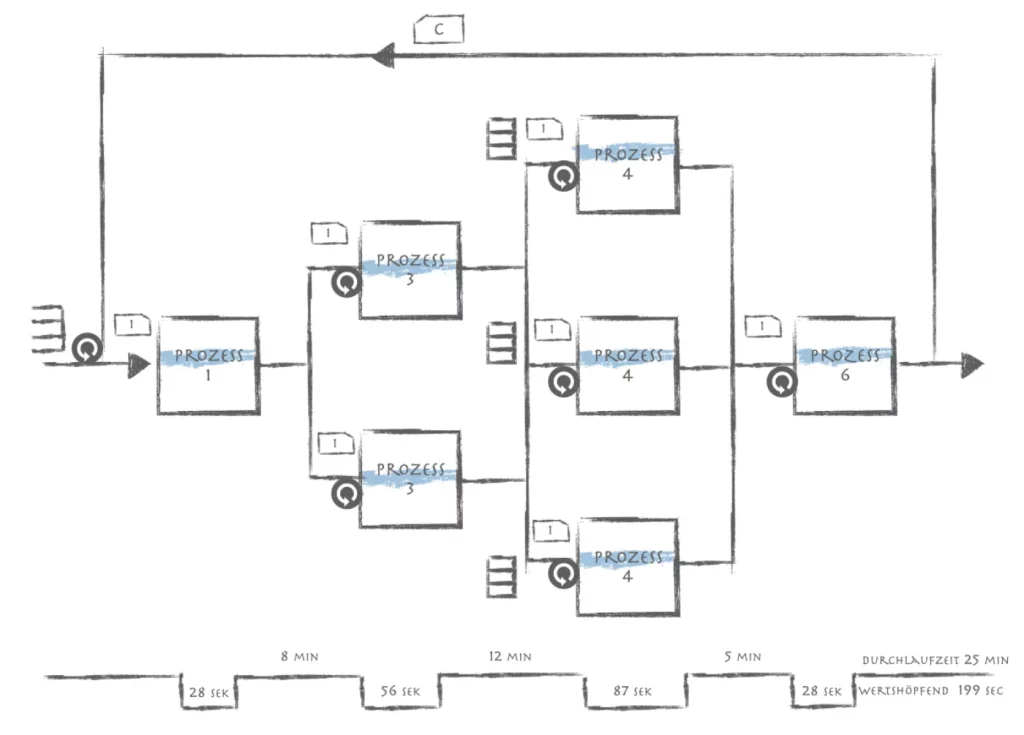
With the help of value stream symbols, you direct the focus on short throughput times and small buffering at the right places. In our example, we have of course incorporated the Smartflow effect with Kanban / ConWiP and, by defining the cycle times, the bottleneck according to ToC (Theory of Constrains).
Now, using this process flow diagram, create a block layout and develop the material flow so that it is clear to each team member how the workpieces get through the machines and the buffers. This gives them a value stream of where their material is flowing.
Conclusion: Computers are wonderful, but ...
Based on the short description in the process planning of your material flow, you can see that the addition of CAD in the course of the production process has now become indispensable, but it must be added at the right time.
If the focus is placed on the wrong things as early as the planning stage of the production facility, serious errors can occur in the manufacturing process that could have been prevented.
When planning production, include the material flow right at the beginning and align the first steps with it. Only when you know how the workpieces progress within your system, what time they require and where buffers need to be installed, can you identify effective combinations that will drastically cut your production time. This gives you a significant advantage over your competitors.
Do you need support in planning your production line or implementing the material flow? Feel free to contact us. We will help you and show you how to become an industry leader with the SmartFlow Effect.