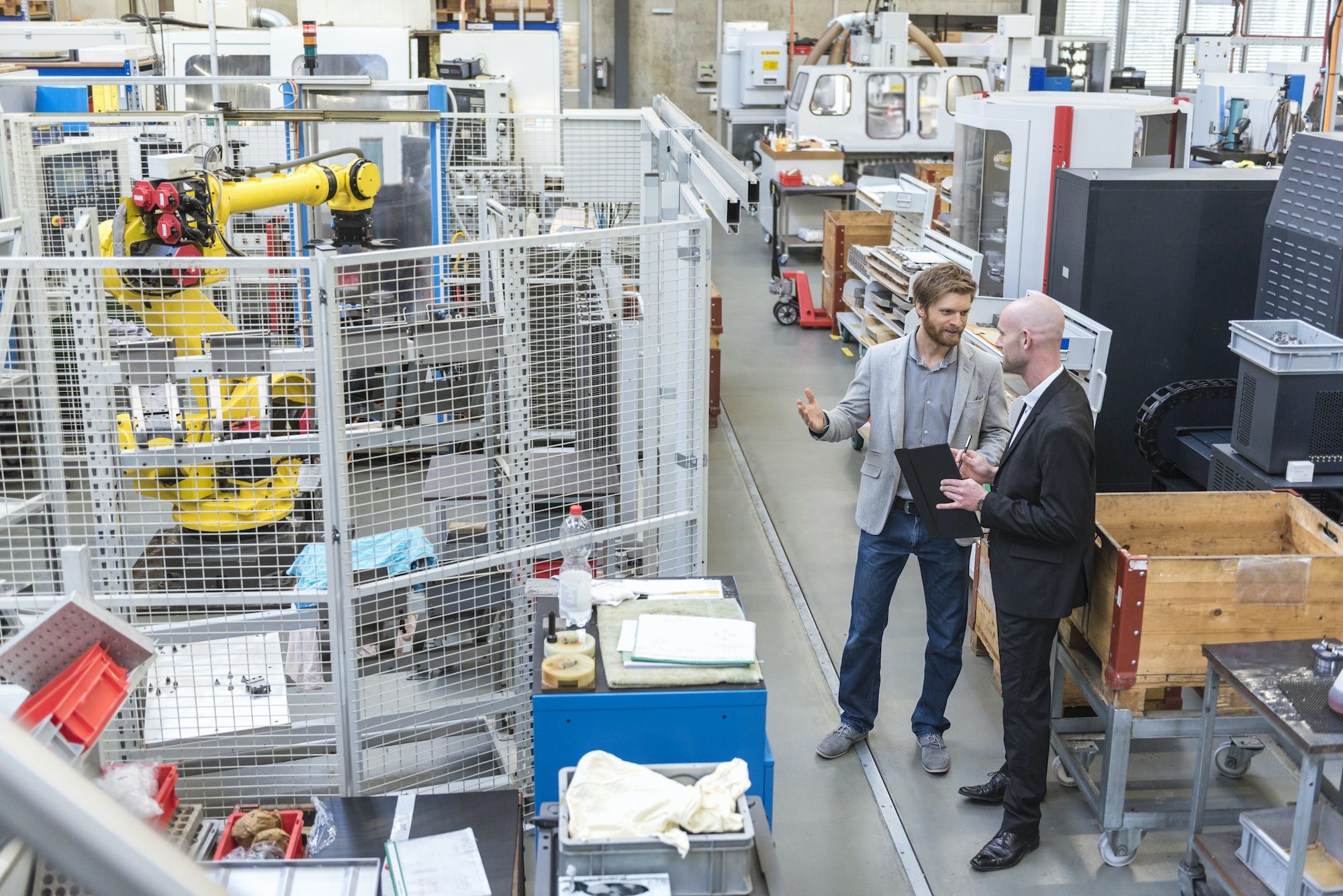
SmartFlow Effect - the hybrid combination
In 1913, when Henry Ford introduced assembly line production for his company, it was an industrial revolution at the time. His employees were able to increase their production speed eightfold and the price of the vehicles produced was cut in half. The automobile became a mass product. And the assembly line became the main component of the industrial revolution.
Today, over 100 years later, assembly line production is still in use. However, it has changed slightly. From the industrial age, via the computer age, we have now arrived in the communication age. Smart solutions within industrial production are desired to optimize production volumes in all industries. However, these do not necessarily have to be found with the help of new technical means. Often, it is enough to look at the roots of production.
In this article, we will show you which all-too-familiar methods are combined and how they can lead to the SmartFlow effect for your production environment.
Industry 4.0 - the panacea?
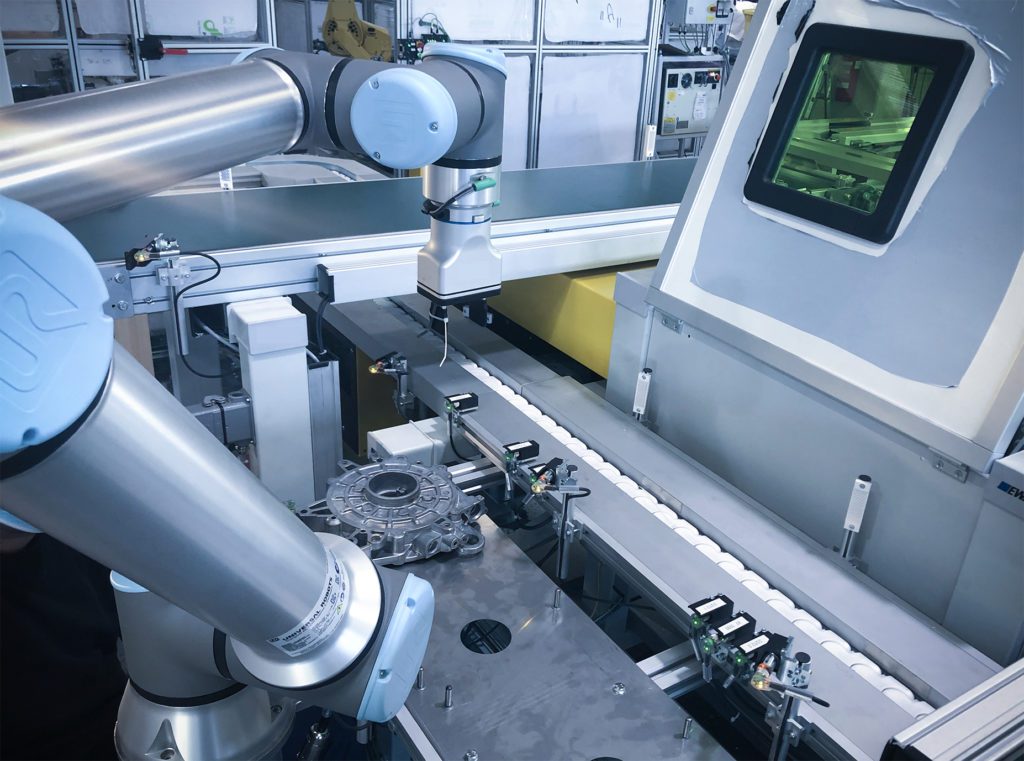
Around 2011, the fourth industrial revolution was proclaimed - Industry 4.0. This is intended to enable companies to network their machines and processes of their industrial production intelligently and across companies. According to Bitcom, 95 percent of companies see i4.0 as an opportunity. Those that do not seize it will inevitably be left behind by the competition. That's absolutely right, but it's also only part of the overall equation.
It's true - Industry 4.0 has ushered in the next industrial revolution and helped propel industry into the communications age. But it would be foolish to believe that this alone will solve the problems and challenges of internal processes in production.
Improving the flow of materials - doing your homework
Poor material flow is not automatically improved by implementing intelligent communication systems within the processes, but often remains the same. What it takes is basic homework that every technician or person in charge must undertake at this point.
Therefore, the first step is to determine how long it basically takes for a workpiece to go through the complete manufacturing cycle, step by step. If the flow time is too long, it will require intervention on your part.
The simplest approach at this point is to reduce the waiting times or excessive amounts of storage between the individual production processes. This also has the advantage that various inefficiencies can be detected at the point that cause the workpieces to have too long a waiting time at certain points in production.
With the SmartFlow effect to the optimal production environment
What happens next once it has been determined where the individual workpieces lie and for how long, and at which points the production process is inefficient? That varies from company to company. Each production company has its own concepts and approaches. However, one that we recommend to you, and which has been proven to achieve the best production results, is a hybrid combination of Kanban, ConWIP and Theory of Constrains. The result of this is what we call the SmartFlow Effect.
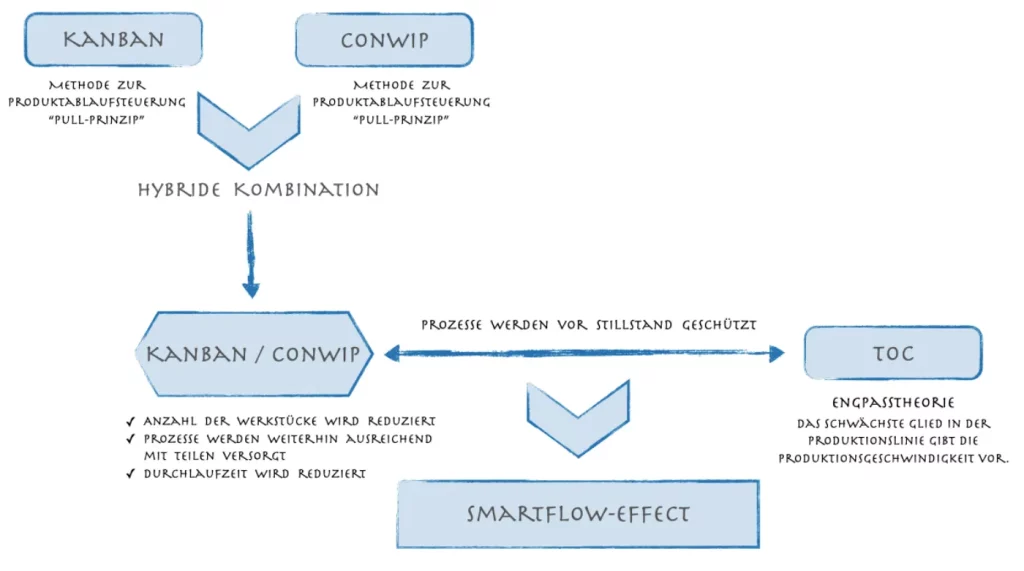
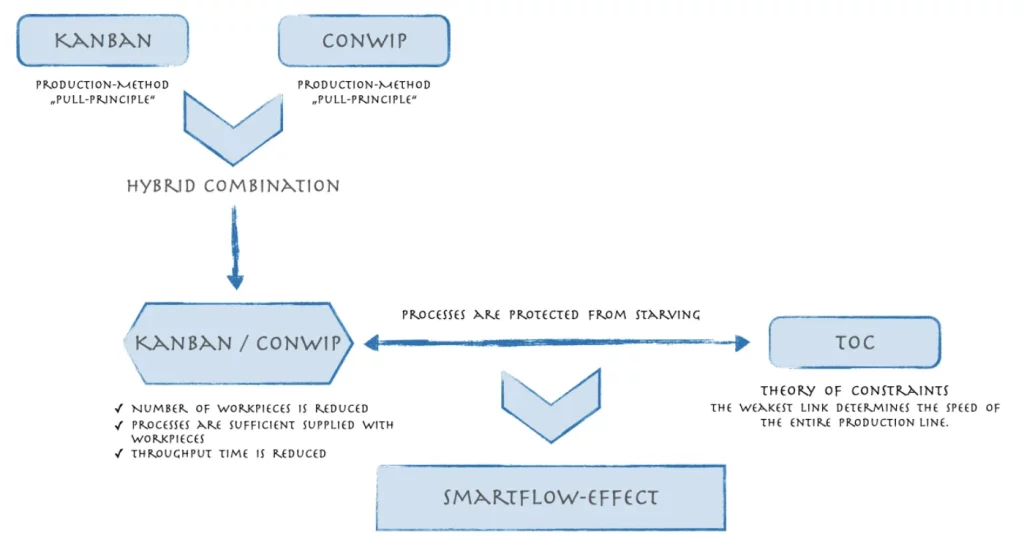
Kanban translated from Japanese means something like card or board and was developed in the 1940s by Taiichi Ōno - the inventor of the Toyota production principle. Kanban is a process control based on the pull principle. Nowadays, it is used in a wide variety of industries, but it originated in production and is still used there today.
ConWIP - also "constant work in progress" - is also a control method based on the pull principle in order to maintain a continuous flow of materials and which also enables lower WIP figures than Kanban.
At first glance, it seems as if a company in the manufacturing industry has to choose one of the two methods. However, this does not have to be the case.
These two methods for product flow control can be combined excellently. Thus, Kanban or ConWIP simply becomes ConWIP/Kanban.
What does this entail?
The ConWIP method - as the name suggests - ensures a constant level of partial stocks within the production line. This means that there is no overproduction at any time. Only when a part leaves the production line ready, a new one is requested.
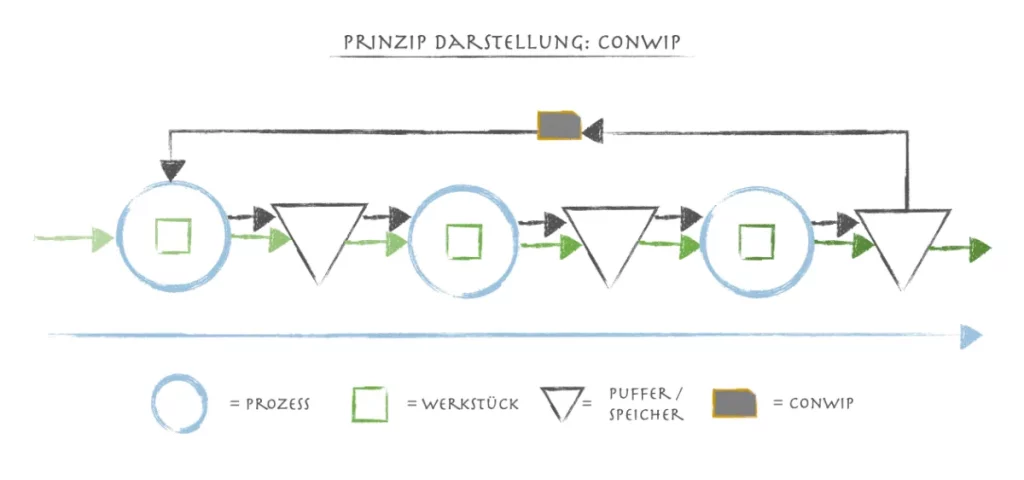
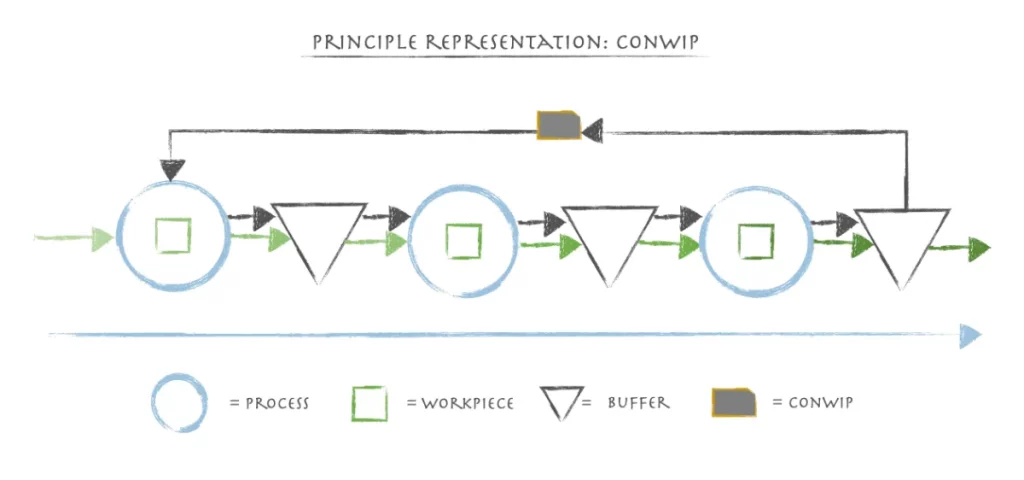
In Kanban, self-controlling control loops are also used, whereby the provision of production parts is oriented to the consumption of the production process.
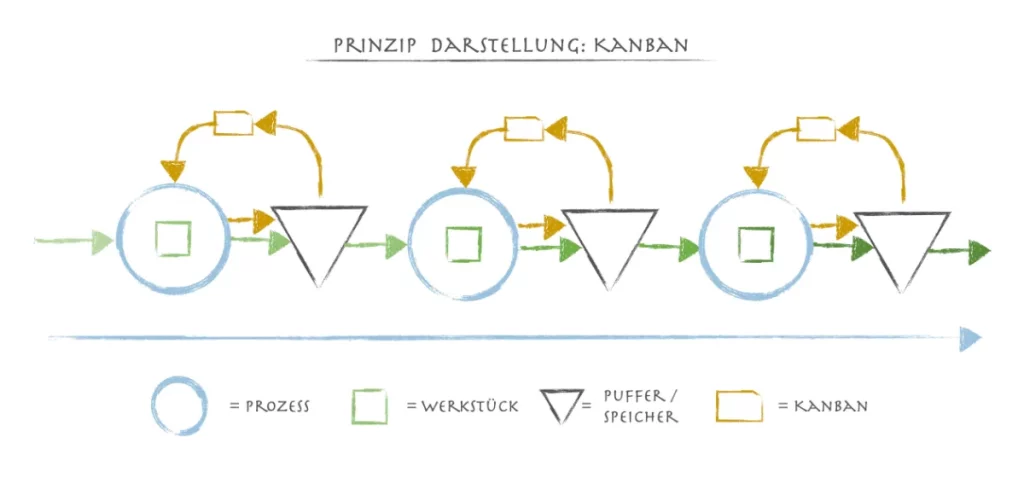
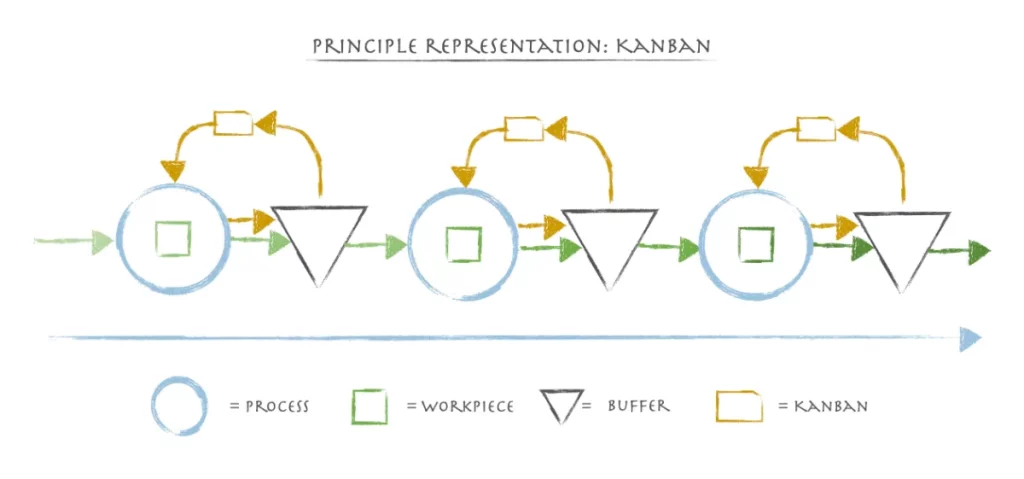
As can be seen here, the individual machines (shown as a circle) produce the workpieces until they finally leave the production line as finished parts. Between the production steps, intermediate storage units are used, which always pass a part on to the next machine when a previous one has left the section.
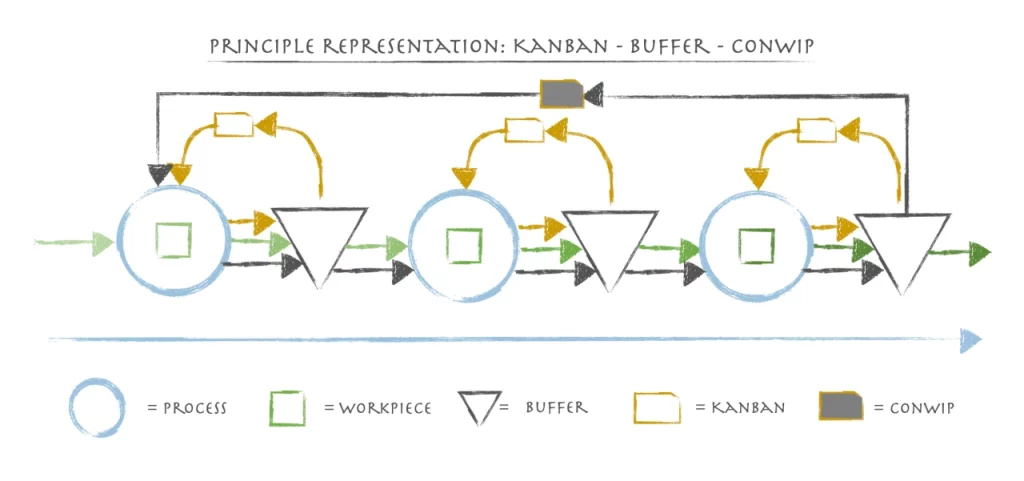
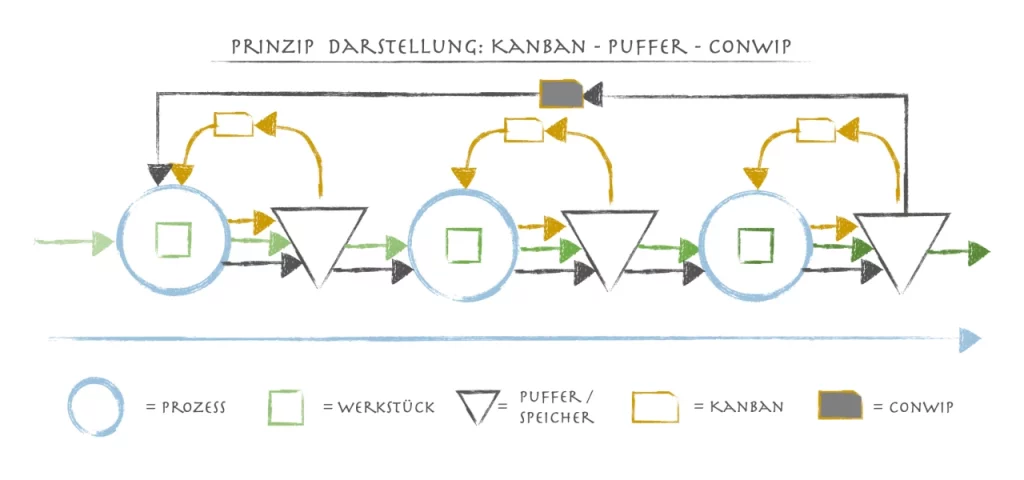
If these two methods are now combined, new parts are not only requested at the end of the production sequence, but already within the sequence - between the individual work steps. As a result, there are always enough parts in the process and the throughput time can be reduced automatically.
Theory of Constrains
The Theory of Constrains, or bottleneck theory, is the third building block for obtaining the SmartFlow effect in the production process.
Every system has a weakest link. A machine that produces the slowest or is the most prone to failure. This weakest link therefore sets the pace for the overall production speed. If this part in the production line is improved, another process takes its place and sets the pace.
However, the production flow dictated by the weakest part is protected from downtime by the ConWIP/Kanban combination, as there are always enough parts in the buffer to draw from the buffer and maintain production in the event of a failure.
To define enough buffer, take the most critical process, make it slower and define how long it should continue to run if the manufacturing processes fail beforehand.
Not either/or, but both/and
As you can see, improving the flow of materials within your production environment is not at all dependent on new technologies. It depends solely on basic calculations and organizations. Both the Kanban and ConWIP principles are familiar to you and may already be in use at your facility. Combine the different methods and identify your weakest link in the production chain and you can set up a smart production flow. The addition of data acquisition and monitoring through Industrie 4.0 technology thus becomes even more effective.
This is the SmartFlow effect!
Would you like to learn more or learn how to achieve the SmartFlow effect within your production as well? Write to us. We will be happy to help you.