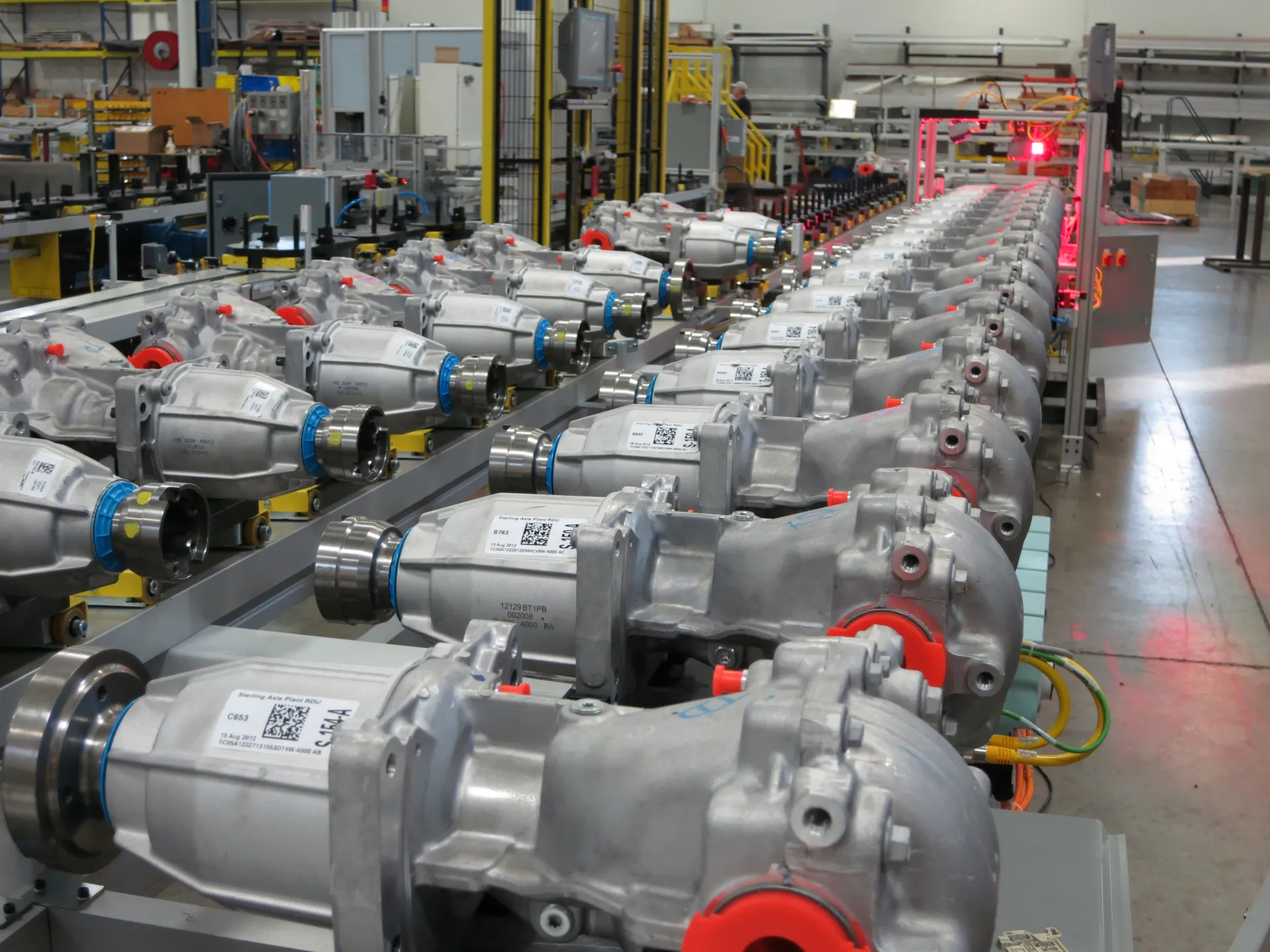
Why material flow is so important ...
In manufacturing, there is always a flow of material. Whether this is intentional or not, or whether this is managed first-class or not. If a certain workpiece exists at the beginning and something else comes out at the end, then this product went through various processes within a material flow. This was already known by the pioneers in the field, Henry Ford and Taichi Ohno, who both used the material flow with their philosophy and optimized it for themselves.
In this article, we'll tell you why material flow is so important and what to look for in management.
In a production facility before our time. The pioneers of material flow.
At the beginning of the 20th century, a number of people played a leading role in the simultaneous upswing of the global economy and permanently changed the nature of production. Each in his own way.
Henry Ford, whose production management laid the foundation for mass production based on conveyor systems, had developed a system at the time that was designed to create added value as quickly as possible. This meant no buffers within the production line, no variants in the product and everything in a prescribed sequence.
"Every customer can have his car painted in any color as long as it is black" is emblematic of the American pioneer's approach. This also works excellently, as long as there are no breakdowns within the production line or the customers have no extra requests or variants to be produced. But it is not that simple.
Taichi Ohno, who created the Toyota Production System, chose a different approach that still meets the needs of modern customers. He focused more on material flow - that is, eliminating disruptions and reducing workpieces in production (WIP) circulation.
Today's so-called "lean" production is characterized by the fact that it is exactly in the customer's cycle and is produced only when there is a direct demand. Also known as the pull principle.
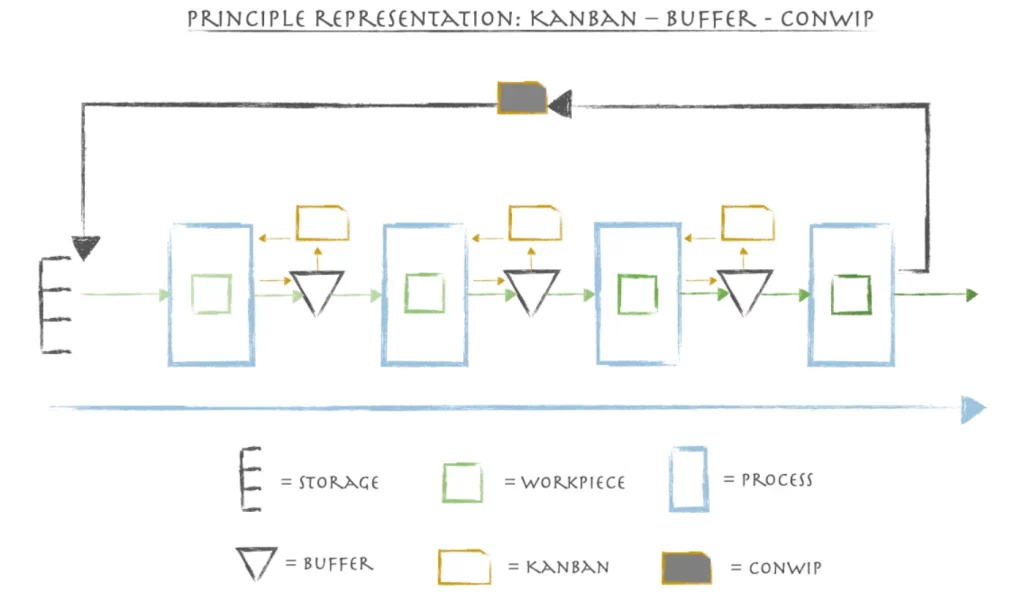
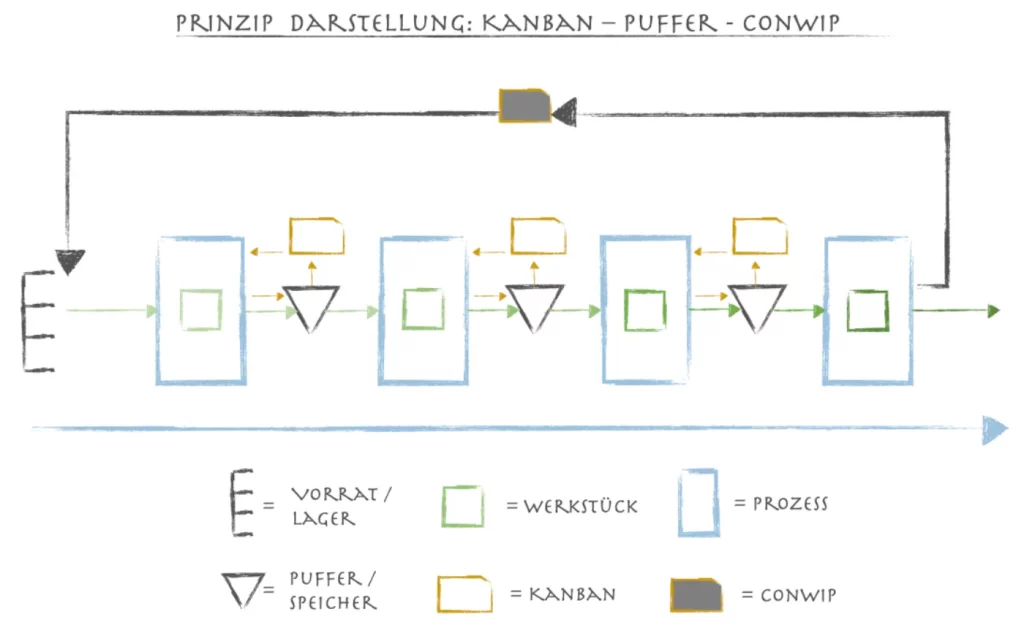
The big goal: speed
The goal of every company in the manufacturing industry must be to turn the respective workpieces into the new and ultimate end product by means of a specific machining, further processing or merging with other parts - quickly at best. Every minute that a product is in the factory and not in the sales department or at the customer's is tied up capital. Therefore, the ultimate goal is also to get the workpieces through the production line as quickly as possible.
Accordingly, the material flow plays an important role at this point.
- How is the production structured?
- Which point in the production is the weakest link?
- Where is there a need for optimization?
- What happens if a machine or employee fails at short notice?
These and many other questions, need to be asked on an ongoing basis to really get the most out of your production facility.
Less work in process for more quality
The fact is: every second that a workpiece spends in intermediate storage generates costs - for warehouse personnel, for logistics in general, and for quality assurance. Stored workpieces can, of course, be defective. Quality control of the parts takes time and money. It is often the case that the quality control part becomes the bottleneck in the entire manufacturing process - the part that is responsible for creating overproduction, and this overproduction will become ever greater if the material flow is not optimized.

In general, therefore, it can be said that the actual pure processing time of the workpieces is only a fraction of how much time the workpieces spend in intermediate storage.

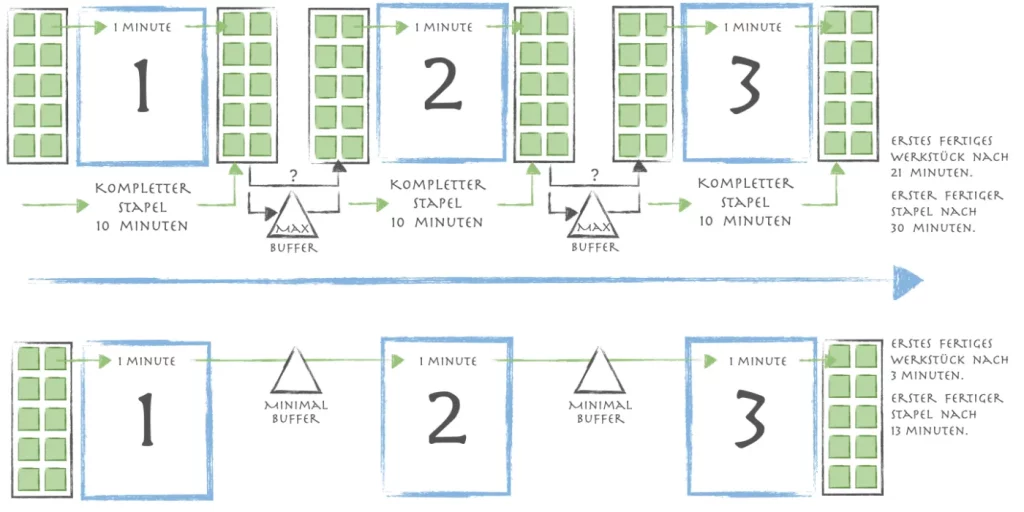
From the chart, you can see how much longer it takes when there are fixed buffers with a number of parts between processes. 21 minutes vs. 3 minutes for the first part and 30 minutes vs. 13 minutes for a complete set of ten parts.
→ WIP influences lead time and throughput
You can find out how to calculate the lead time of the workpieces in the Valuestream here .
Buffer in the material flow can also be good
However, it would be wrong to say that intermediate storage or buffers are generally bad for profitability. After all, with the right buffers in the right places to absorb fluctuations, the flow of materials and thus the value added of the entire production can be improved. This in turn leads to an advantage over competitors, as it reduces the overall lead time.
The fundamental idea should always be that a flawless flow of materials between the individual production processes within a production line is the most efficient way to shorten production and delivery times.
Not the individual machine, but the big picture.
Thus, the focus on improving individual machines makes little sense if the production steps upstream and downstream are not coordinated with them. The result would therefore be rather counterproductive. It can happen that the new, improved machine produces so quickly beyond the demand that larger quantities of workpieces accumulate at other points and the problem mentioned above occurs again - too long waiting times of workpieces within production and thus tied up capital in the plant.
If, on the other hand, the big picture is considered, it is possible to optimize systematically at several points, so that the individual steps are always coordinated with each other - in line with the respective capacity and taking the bottleneck into account.
Conclusion: The SmartFlow Effect
Using the bottleneck theory (ToC), the weakest link in the production line is identified, preferably even determined, with the help of which the overall speed of production is specified. With the help of a hybrid pull combination of the two lean methods Kanban and CONWIP, the number of workpieces in the process is reduced in a controlled manner, which means that the throughput time is also reduced and all processes are still supplied with workpieces.
This is how you achieve the so-called SmartFlow effect. Completely without initial investments in intelligent AI systems or changes to the production speeds of individual machines.
With a simple and intelligent approach to the production line, material flow can be improved, production increased and competitiveness enhanced.
Would you like to learn more about how the SmartFlow Effect works? Feel free to contact us. We will explain how it works and how you can achieve it too.