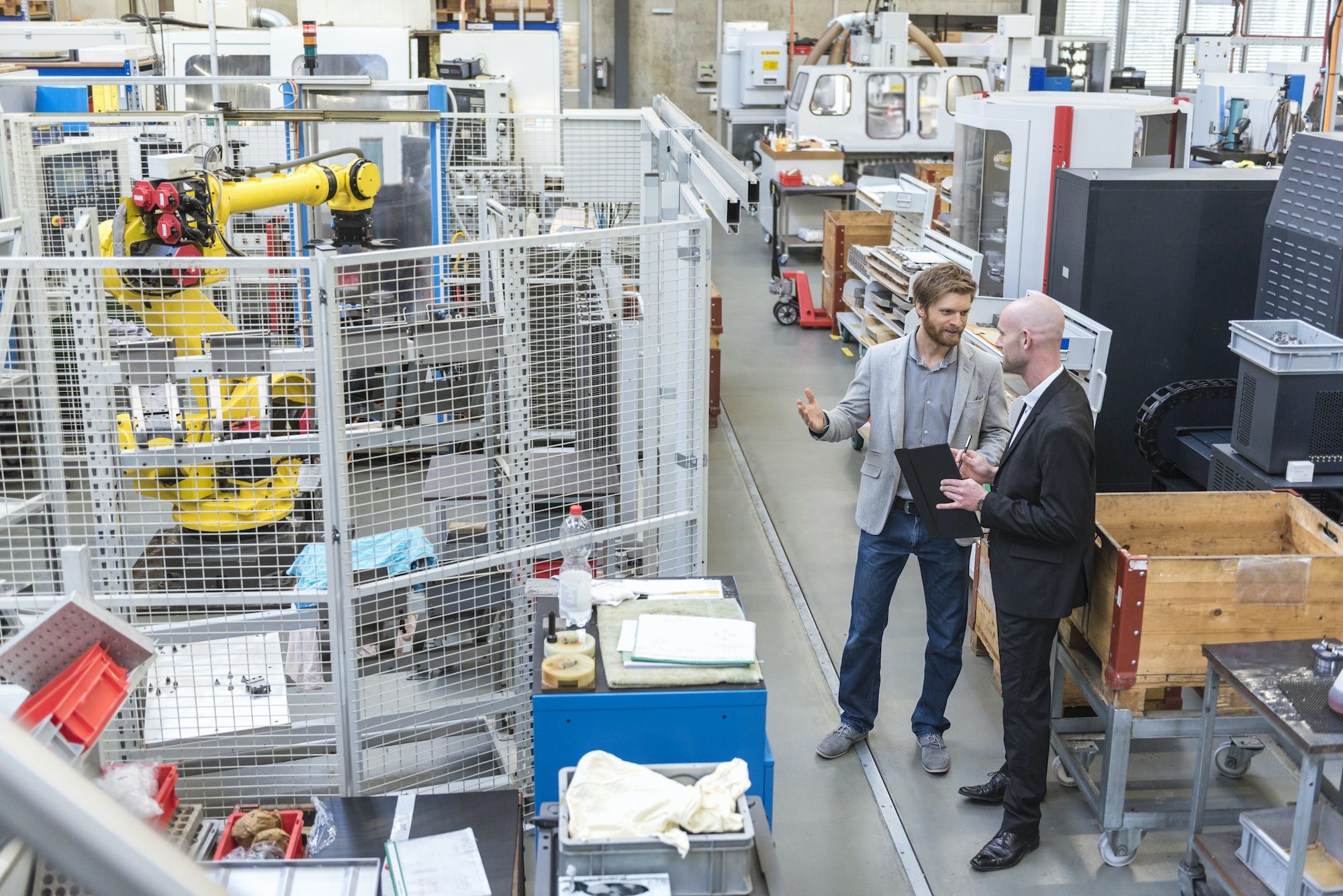
SmartFlow-Effect – die hybride Kombination
1913, als Henry Ford die Fließbandproduktion für sein Unternehmen einführte, war das damals eine industrielle Revolution. Seine Mitarbeiter konnten ihre Produktionsgeschwindigkeit verachtfachen und der Preis für die hergestellten Fahrzeuge wurde um die Hälfte reduziert. Das Automobil wurde zum Massenprodukt. Und das Fließband zum Hauptbestandteil der industriellen Revolution.
Heute, über 100 Jahre später, ist die Fließbandfertigung noch immer im Einsatz. Jedoch leicht verändert. Vom Industriezeitalter, über das Computerzeitalter sind wir mittlerweile im Kommunikationszeitalter angekommen. Smarte Lösungen innerhalb der industriellen Produktion sind gewünscht, um das Produktionsvolumen in allen Branchen zu optimieren. Diese müssen jedoch nicht zwangsläufig mithilfe neuer technischer Mittel gefunden werden. Oftmals reicht auch der Blick zu den Wurzeln der Produktion.
In diesem Artikel zeigen wir Ihnen, welche allseits bekannten Methoden miteinander kombiniert werden und wie diese zum SmartFlow-Effect für Ihre Produktionsumgebung führen können.
Industrie 4.0 – das Allheilmittel?
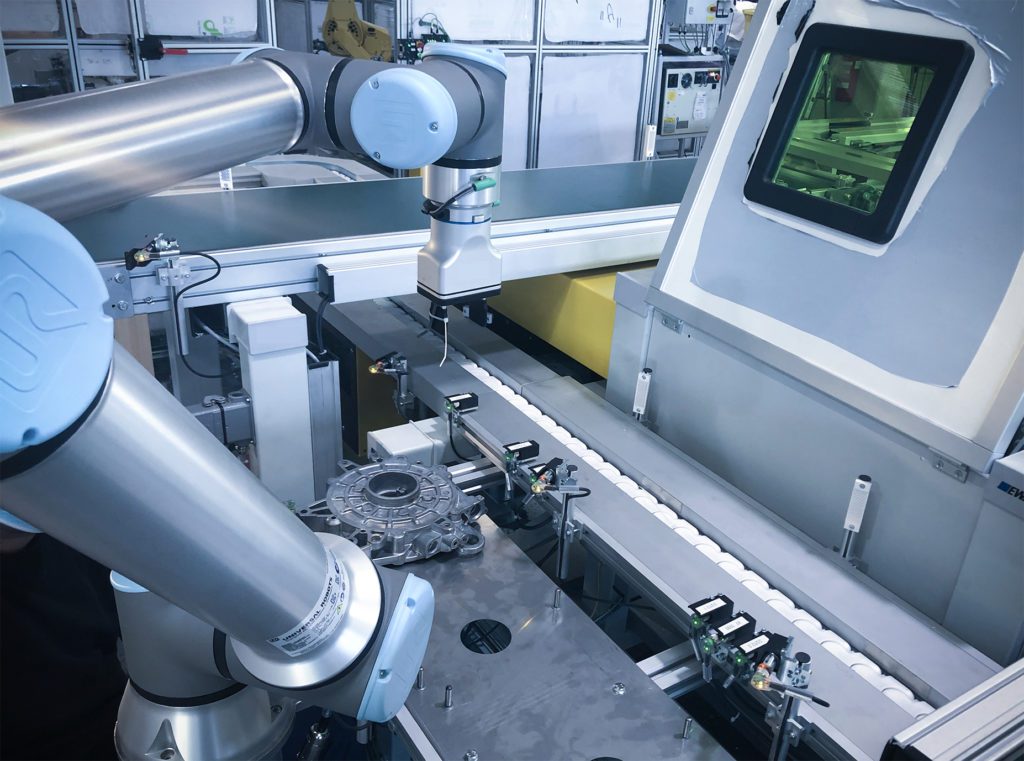
Um das Jahr 2011 wurde die vierte industrielle Revolution ausgerufen – die Industrie 4.0. Damit soll es den Unternehmen ermöglicht werden, ihre Maschinen und Abläufe ihrer industriellen Produktion intelligent und unternehmensübergreifenden miteinander zu vernetzen. Laut Bitcom sehen 95 Prozent der Unternehmen i4.0 als Chance. Wer diese nicht ergreift, wird zwangsläufig von der Konkurrenz abgehängt. Das ist vollkommen richtig, aber auch nur ein Teil der Gesamtgleichung.
Es stimmt – Industrie 4.0 hat die nächste industrielle Revolution eingeleitet und die Industrie mit in das Kommunikationszeitalter befördert. Doch wäre es töricht zu glauben, dass sich Probleme und Herausforderungen interner Prozesse in der Produktion allein damit beheben lassen.
Verbesserung des Materialflusses – die Hausaufgaben machen
Ein schlechter Materialfluss wird nicht automatisch durch die Implementierung intelligenter Kommunikationssysteme innerhalb der Prozesse verbessert, sondern bleibt oftmals gleich. Was es benötigt, sind grundlegende Hausaufgaben, die jeder Techniker oder Verantwortliche an diesem Punkt unternehmen muss.
Daher muss zu Beginn erst einmal ermittelt werden, wie lang es grundsätzlich dauert, bis ein Werkstück Schritt für Schritt den kompletten Herstellungszyklus durchlaufen hat. Ist die Durchfluss-Zeit zu lang, benötigt es den Eingriff Ihrerseits.
Der einfachste Ansatz an der Stelle ist es, die Wartezeiten bzw. zu große Speichermengen zwischen den einzelnen Produktionsprozessen zu reduzieren. Dies hat zudem den Vorteil, dass an dem Punkt diverse Ineffizienzen entdeckt werden können, die dafür sorgen, dass die Werkstücke eine zu lange Wartezeit an bestimmten Stellen der Produktion haben.
Mit dem SmartFlow-Effect zur optimalen Produktionsumgebung
Was passiert als Nächstes, wenn ermittelt wurde, wo die einzelnen Werkstücke wie lange liegen und an welchen Stellen der Produktionsablauf ineffizient ist? Das ist von Unternehmen zu Unternehmen verschieden. Jede Produktionsfirma hat seine eigenen Konzepte und Herangehensweisen. Eine, dir wir Ihnen jedoch ans Herz legen, und die nachweislich die besten Produktionsergebnisse erzielt, ist eine hybride Kombination aus Kanban, ConWIP und Theory of Constrains. Das Ergebnis daraus nennen wir den SmartFlow-Effect.
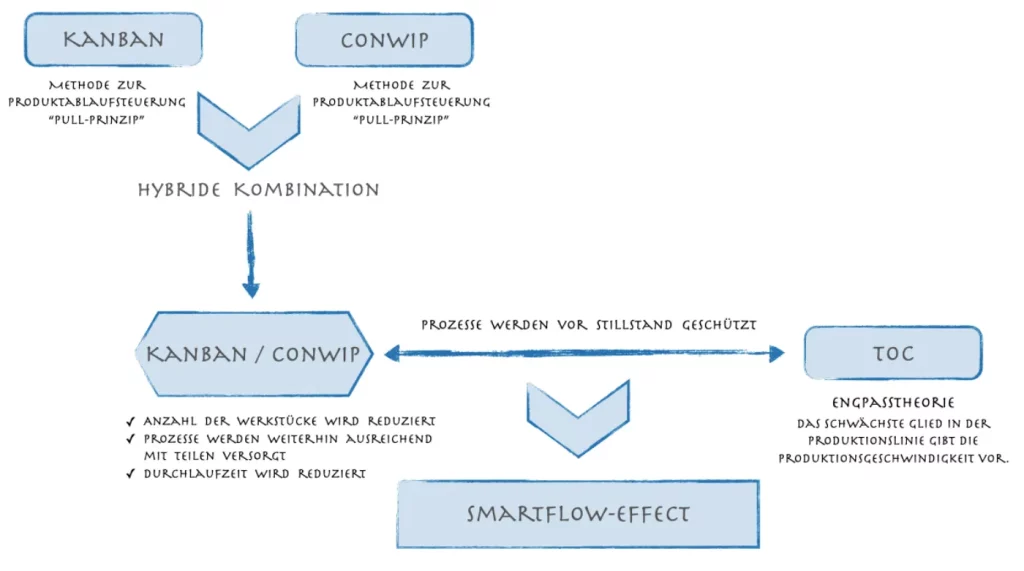
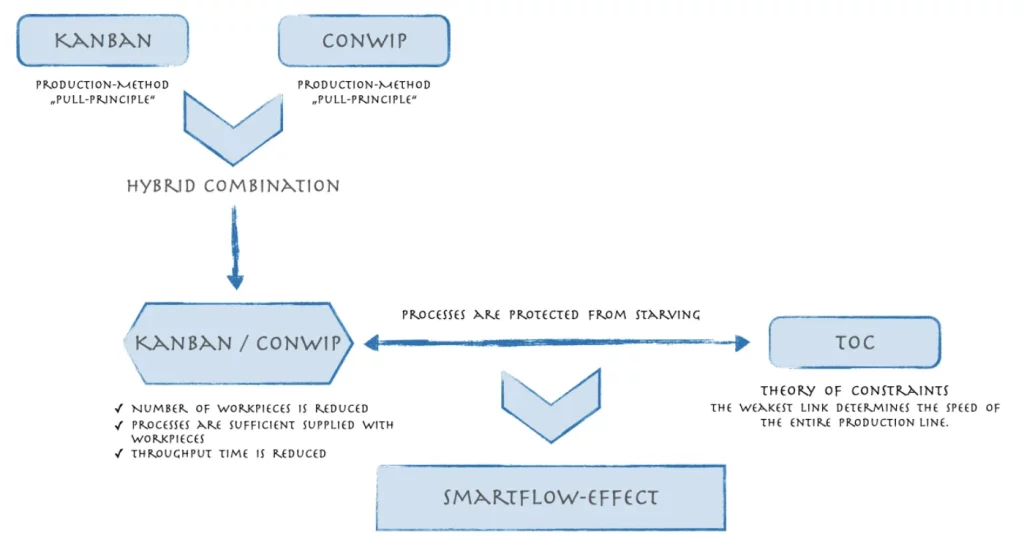
Kanban heißt aus dem Japanischen übersetzt so viel, wie Karte oder Tafel und wurde in den 1940er-Jahren von Taiichi Ōno – dem Erfinder des Toyota-Produktionsprinzip – entwickelt. Kanban ist eine Ablaufsteuerung nach dem Pull-Prinzip. Es findet heutzutage in verschiedensten Branchen seine Anwendung, hatte seinen Ursprung jedoch in der Produktion und wird dort auch heute noch eingesetzt.
ConWIP – auch „constant work in progress“ – ist ebenfalls ein Steuerverfahren auf Basis des Pull-Prinzips, um einen kontinuierlichen Materialfluss zu erhalten und der dazu auch noch geringere WIP-Zahlen ermöglicht als Kanban.
Auf den ersten Blick scheint es so, als müsste man sich als Unternehmen in der Fertigungsindustrie für eine der beiden Methoden entscheiden. Jedoch muss das nicht sein.
Diese beiden Methoden zur Produktablaufsteuerung lassen sich hervorragend kombinieren. So wird aus Kanban oder ConWIP ganz einfach ConWIP/Kanban.
Was hat das zur Folge?
Die ConWIP-Methode sorgt – wie der Name vermuten lässt – für ein konstantes Niveau von Teilbeständen innerhalb der Fertigungslinie. Somit entsteht zu keiner Zeit eine Überproduktion. Erst wenn ein Teil fertig die Produktionslinie verlässt, wird ein neues angefordert.
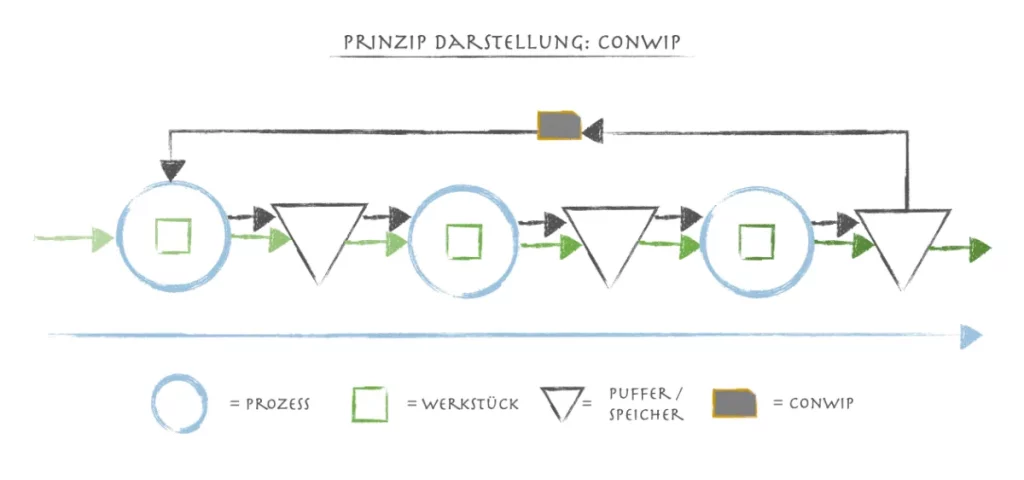
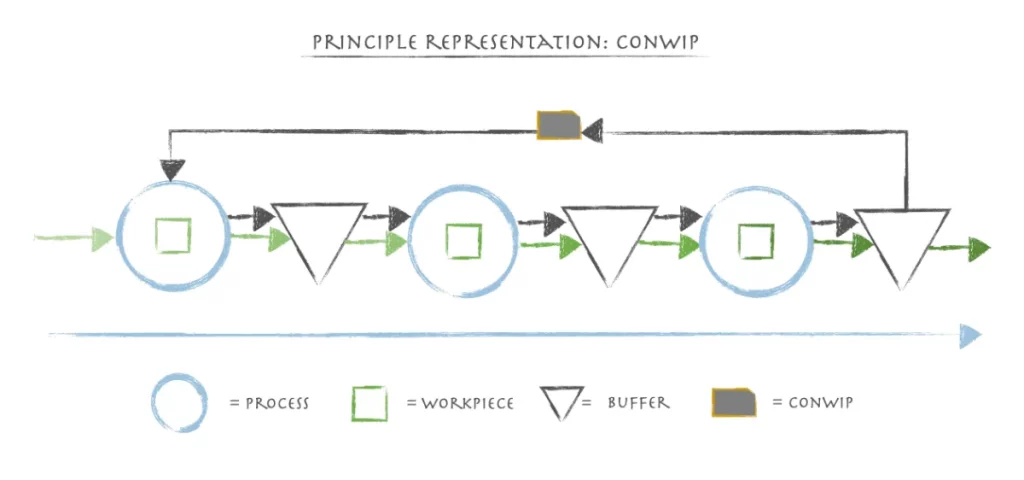
Bei Kanban werden ebenfalls selbststeuernde Regelkreise eingesetzt, wobei sich die Bereitstellung der Fertigungsteile am Verbrauch des Produktionsablaufs orientiert.
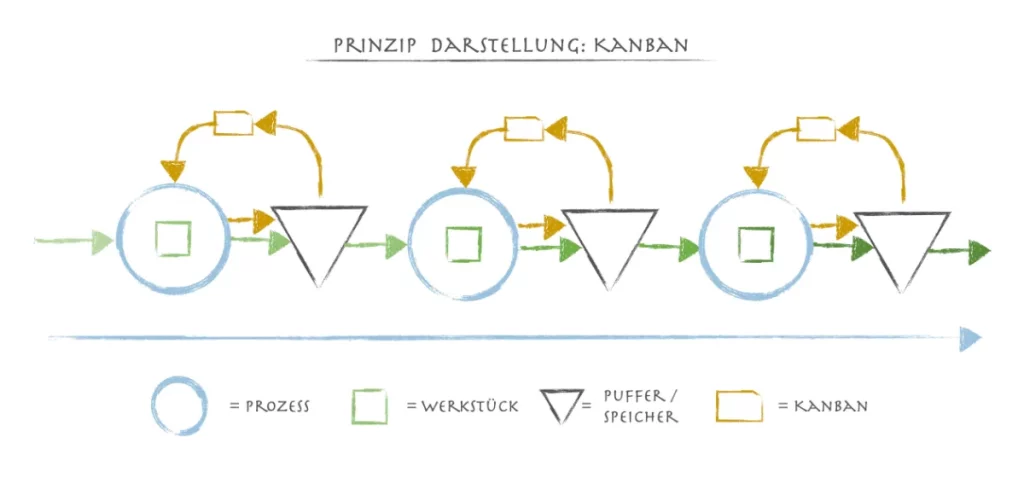
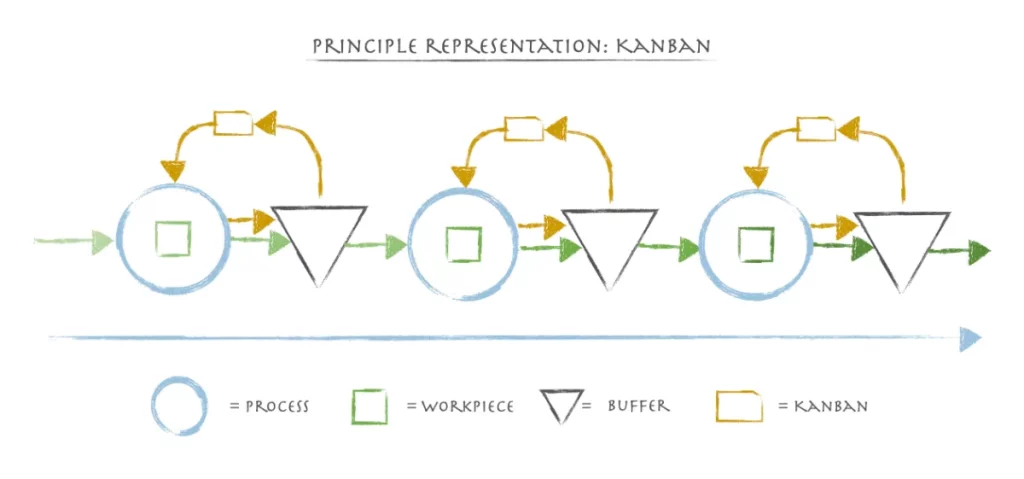
Wie hier zu erkennen, werden über die einzelnen Maschinen (als Kreis dargestellt) die Werkstücke produziert, bis sie am Ende als fertige Teile die Fertigung verlassen. Zwischen den Produktionsschritten werden Zwischenspeicher eingesetzt, die immer ein Teil an die nächste Maschine weitergeben, wenn ein vorheriges den Abschnitt verlassen hat.
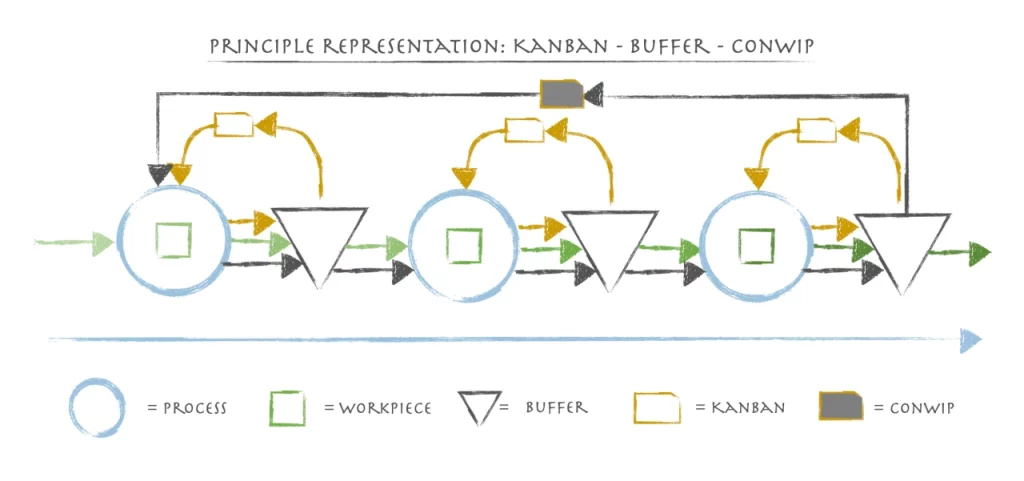
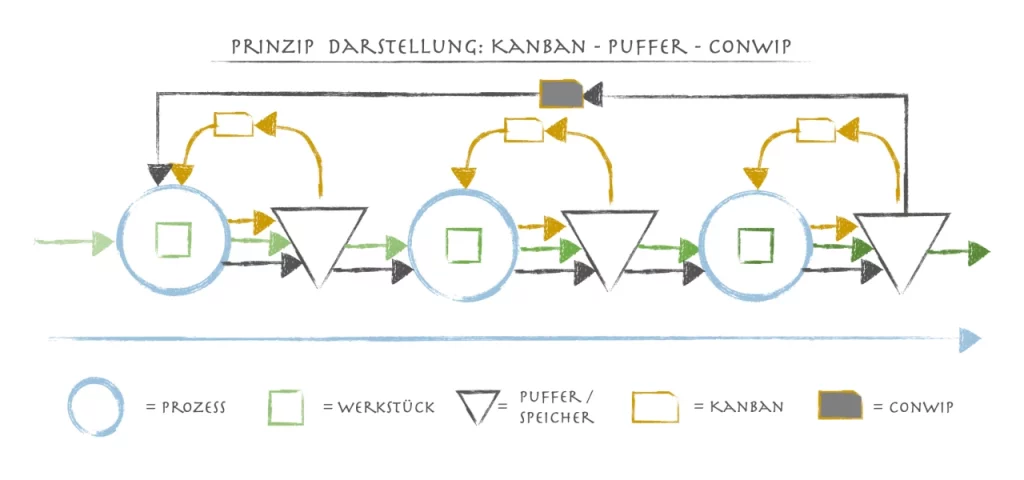
Werden diesen beiden Methoden nun kombiniert, werden nicht nur am Ende des Produktionsablaufs neue Teile angefordert, sondern bereits innerhalb des Ablaufs – zwischen den einzelnen Arbeitsschritten. Dies hat zur Folge, dass sich immer genügend Teile im Prozess befinden und die Durchlaufzeit automatisch reduziert werden kann.
Theory of Constrains
Die Theory of Constrains oder auch Engpasstheorie ist der dritte Baustein, um den SmartFlow-Effect im Produktionsablauf zu erhalten.
Jedes System hat ein schwächstes Glied. Eine Maschine, die am langsamsten produziert oder am anfälligsten für Ausfälle ist. Dieses schwächste Glied gibt daher den Takt der gesamten Produktionsgeschwindigkeit an. Wird dieser Part in der Fertigungslinie verbessert, nimmt ein anderer Prozess den Platz ein und gibt den Takt vor.
Der vom schwächsten Part vorgegebene Produktionsablauf wird jedoch durch die ConWIP/Kanban Kombination vor Stillstand geschützt, da sich stets genügend Teile in den Zwischenspeichern befinden, um im Falle eines Ausfalls vom Puffer zehren und die Produktion aufrechterhalten zu können.
Um genügend Zwischenspeicher zu definieren, nehmen Sie sich den kritischsten Prozess vor, machen ihn langsamer und definieren Sie, wie lang dieser weiterlaufen soll, wenn die Fertigungsprozesse vorher einmal ausfallen sollten.
Kein entweder/oder, sondern sowohl/als auch
Wie Sie erkennen, steht die Verbesserung des Materialflusses innerhalb Ihrer Produktionsumgebung keineswegs in Abhängigkeit neuer Technologien. Es kommt einzig und allein auf grundlegende Berechnungen und Organisationen an. Sowohl das Kanban- als auch das ConWIP-Prinzip sind Ihnen ein Begriff und möglicherweise bereits bei Ihnen in Benutzung. Kombinieren Sie die verschiedenen Methoden miteinander und ermitteln Sie Ihr schwächstes Glied in der Produktionskette, können Sie einen smarten Produktionsablauf einrichten. Die Hinzunahme von Datenerfassung und Überwachung durch Industrie 4.0-Technologie wird somit noch effektiver.
Das ist der SmartFlow-Effect!
Möchten Sie mehr darüber erfahren oder lernen, wie Sie den SmartFlow-Effect auch innerhalb Ihrer Produktion erreichen? Schreiben Sie uns. Wir helfen Ihnen gerne weiter.